Method for preparing black cobalt-based ceramic pigment by utilizing tannery sludge
A technology of black ceramic pigment and tannery sludge, which is applied in the production, application, household appliances and other directions of ceramic materials, can solve problems such as mass production and application limitations, achieve significant economic and social benefits, reduce costs, and reduce the cost of The effect of increasing the degree of
- Summary
- Abstract
- Description
- Claims
- Application Information
AI Technical Summary
Problems solved by technology
Method used
Image
Examples
example 1
[0012] A method for preparing cobalt-based black ceramic pigments from tannery sludge, which uses tannery sludge to completely replace chromium oxide, and its weight percentage composition is: 40% of tannery sludge, 30% of iron oxide red, 5% of nickel oxide % and cobalt oxide 25%; the tannery sludge is calcined (the calcining temperature is 1040°C in a non-oxidizing atmosphere) and ball-milled to a fineness of 300 mesh for later use, and then mixed with other components, calcined, and sieved ( 300 mesh) to obtain the product, wherein the calcination temperature is 1300 ° C, and the heat preservation is 120min.
[0013] Add 5% of the above black colorant to commercial lead-based frit, add 1% carboxymethyl cellulose, and wet grind to obtain a ceramic glaze. The glaze is applied to the ceramic sample plate, calcined at a high temperature of 1200 ° C, and kept for 30 minutes.
example 2
[0015] A method for preparing cobalt-based black ceramic pigments from tannery sludge, which uses tannery sludge to completely replace chromium oxide, and its weight percentage composition is: 45% of tannery sludge, 30% of iron oxide red, and 5% of nickel oxide % and cobalt oxide 20%; the tannery sludge is calcined (the calcining temperature is 1040°C in a non-oxidizing atmosphere) and ball-milled to a fineness of 300 mesh for later use, and then mixed with other components, calcined, and sieved ( 300 mesh) to obtain the product, wherein the calcination temperature is 1300 ° C, and the heat preservation is 120min.
[0016] Add 5% of the above black colorant to commercial lead-based frit, add 1% carboxymethyl cellulose, and wet grind to obtain a ceramic glaze. The glaze is applied to the ceramic sample plate, calcined at a high temperature of 1200 ° C, and kept for 30 minutes.
example 3
[0018] A method for preparing cobalt-based black ceramic pigments from tannery sludge, which uses tannery sludge to completely replace chromium oxide, and its weight percentage composition is: 55% of tannery sludge, 25% of iron oxide red, and 5% of nickel oxide % and cobalt oxide 15%; the tannery sludge is calcined (the calcining temperature is 1040°C in a non-oxidizing atmosphere) and ball-milled to a fineness of 300 mesh for later use, and then mixed with other components, calcined, and sieved ( 300 mesh) to obtain the product, wherein the calcination temperature is 1300 ° C, and the heat preservation is 120min.
[0019] Add 5% of the above black colorant to commercial lead-based frit, add 1% carboxymethyl cellulose, and wet grind to obtain a ceramic glaze. The glaze is applied to the ceramic sample plate, calcined at a high temperature of 1200 ° C, and kept for 30 minutes. Example 4
PUM
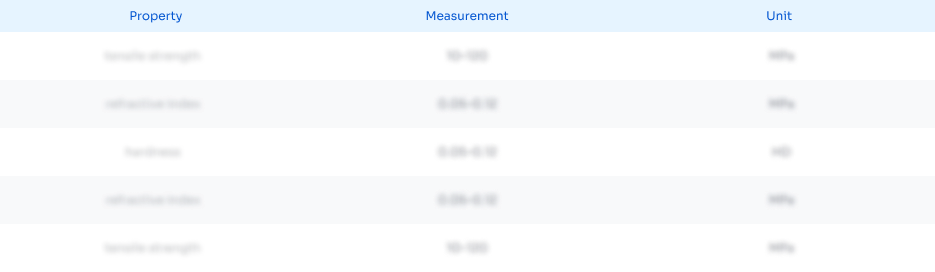
Abstract
Description
Claims
Application Information

- R&D
- Intellectual Property
- Life Sciences
- Materials
- Tech Scout
- Unparalleled Data Quality
- Higher Quality Content
- 60% Fewer Hallucinations
Browse by: Latest US Patents, China's latest patents, Technical Efficacy Thesaurus, Application Domain, Technology Topic, Popular Technical Reports.
© 2025 PatSnap. All rights reserved.Legal|Privacy policy|Modern Slavery Act Transparency Statement|Sitemap|About US| Contact US: help@patsnap.com