Pultrusion device and preparation process for high-strength FRP materials
A high-strength, pultrusion die technology, applied in the field of high-strength FRP material pultrusion process, can solve the problems of low strength, inability to give full play to the high-strength performance of fibers, and limit the application and promotion of FRP materials, so as to ensure fluidity and avoid damage to fiber bundles , to achieve the effect of linearity
- Summary
- Abstract
- Description
- Claims
- Application Information
AI Technical Summary
Problems solved by technology
Method used
Image
Examples
Embodiment 1
[0038] Example 1: A pultrusion device for high-strength FRP materials, used to prepare FRP plate pultrusion products.
[0039] The bobbins 2 are placed on the creel 1, and the fiber rovings 3 are drawn out from the creel 1 and passed through the plastic buckle 5 of the first yarn collecting plate 4 bundle by bundle. The dipping tank 6 is filled with a uniformly mixed resin and filler mixture glue 9, and a first heating device 7 is installed below the dipping tank 6 for heating the glue, improving the fluidity of the glue, and ensuring that the fiber roving is fully impregnated. The first yarn-pressing drum 8 and the second yarn-pressing drum 10 are installed between the first yarn-collecting board 4 and the second yarn-collecting board 12 to lower the position of the fiber roving so that the fiber roving is fully immersed in the glue solution 9, and the third yarn-pressing drum 11 is located at the front and upper part of the second pressing cylinder 10, and is used to lead th...
Embodiment 2
[0044] Example 2: A pultrusion device for high-strength FRP materials, used to prepare FRP tendon pultrusion products.
[0045] In this embodiment, except for the first yarn collecting board, the second yarn collecting board and the third yarn collecting board, the others are the same as those in embodiment 1.
[0046] In this embodiment, the number of holes on the traction first yarn collecting board 4, the second yarn collecting board 12 and the third yarn collecting board 13 decreases successively, and the holes take the center point as the center of the circle and are distributed circumferentially, such as Figure 7 , 8 ,9. The diameter of the entrance end of the curved wedge-shaped groove 15 is 1.5-2.0d (the design diameter of the FRP rib), and the cross-section diameters from 20mm near the exit end to the exit end are all d.
PUM
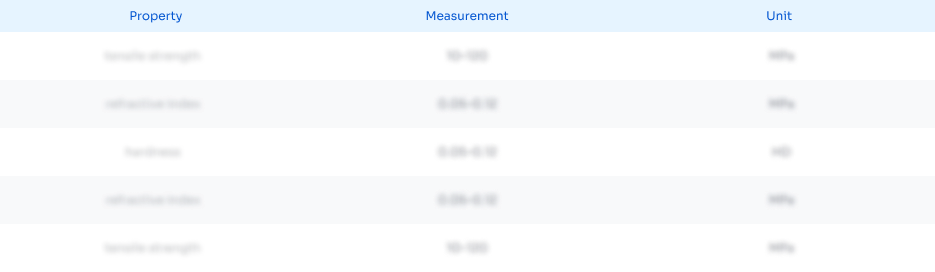
Abstract
Description
Claims
Application Information

- Generate Ideas
- Intellectual Property
- Life Sciences
- Materials
- Tech Scout
- Unparalleled Data Quality
- Higher Quality Content
- 60% Fewer Hallucinations
Browse by: Latest US Patents, China's latest patents, Technical Efficacy Thesaurus, Application Domain, Technology Topic, Popular Technical Reports.
© 2025 PatSnap. All rights reserved.Legal|Privacy policy|Modern Slavery Act Transparency Statement|Sitemap|About US| Contact US: help@patsnap.com