Extinction master batch for plastics and preparation method thereof
A matting masterbatch and plastic technology, applied in the field of plastic processing, can solve the problems of different crushing degrees of matting masterbatches, hindering the stable use effect of matting masterbatches, and affecting the overall performance of matting masterbatches. Improve the shear rate and shear quality, and meet the effect of the shearing effect
- Summary
- Abstract
- Description
- Claims
- Application Information
AI Technical Summary
Problems solved by technology
Method used
Image
Examples
Embodiment approach
[0033] As an embodiment of the present invention, a vibrating block 531 is provided on the screen hole 53, the vibrating block 531 is in the shape of an inverted circular platform, the vibrating block 531 divides the sieve hole 53 into a ring, and the bottom of the vibrating block 531 is provided with a counterweight Plate 532; the counterweight plate 532 is slidingly installed on the bottom of the sieve hole 53; during work, the particles of the main body 1 sheared by the shearing plate 4 in different degrees fall into the sieve hole 53, due to the shape of the main body 1 particles sheared Different, so that the particles of the main body 1 on the screen hole 53 interfere with each other, causing blockage to the screen hole 53 and affecting the screening of the screen cloth 5; through the vibration block 531 arranged on the screen hole 53, the vibration of the screen cloth 5 , so that the vibrating block 531 vibrates up and down in the screen hole 53 under the action of the c...
PUM
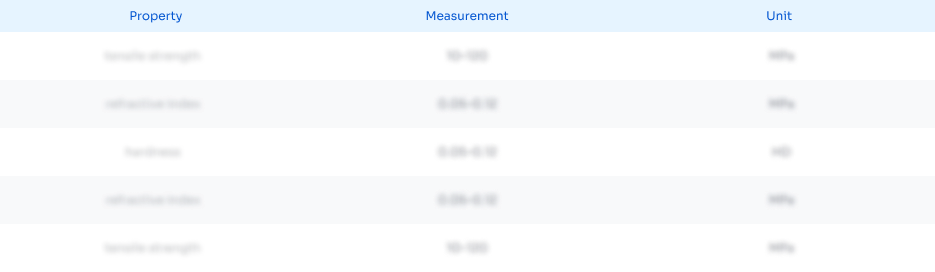
Abstract
Description
Claims
Application Information

- R&D
- Intellectual Property
- Life Sciences
- Materials
- Tech Scout
- Unparalleled Data Quality
- Higher Quality Content
- 60% Fewer Hallucinations
Browse by: Latest US Patents, China's latest patents, Technical Efficacy Thesaurus, Application Domain, Technology Topic, Popular Technical Reports.
© 2025 PatSnap. All rights reserved.Legal|Privacy policy|Modern Slavery Act Transparency Statement|Sitemap|About US| Contact US: help@patsnap.com