Impact-resistant strong-adhesion type powder coating material and preparation method thereof
A powder coating and impact technology, applied in powder coatings, polyester coatings, epoxy resin coatings, etc., can solve the problems of poor impact resistance and adhesion of coatings, and achieve strong impact resistance, high hardness, excellent The effect of adhesion
- Summary
- Abstract
- Description
- Claims
- Application Information
AI Technical Summary
Problems solved by technology
Method used
Image
Examples
preparation example Construction
[0026] Another aspect of the present invention provides a method for preparing the aforementioned impact-resistant strong adhesion powder coating, the method comprising the following steps:
[0027] (1) melt mixing and grinding modified epoxy resin, modified polyester resin and curing agent;
[0028] (2) Add polycarbonate resin, styrene-acrylonitrile resin and leveling agent to the product obtained in step (1), melt and mix;
[0029] (3) Add pigment to the product obtained in step (2), grind after stirring.
[0030] In order to improve the impact resistance and adhesion of the powder coating of the present invention, step (1) and step (3) also include passing the product after grinding through a 50-80 mesh screen; specifically, for example, it can be 50 mesh, 60 mesh, 70 mesh, 80 mesh and any value in the range formed by any two of these point values; preferably, step (1) and step (3) also include passing the ground product through a 65 mesh screen.
Embodiment 1
[0033] (1) the glycidyl ester type epoxy resin of 10 weight parts, the acrylic acid modified polyester resin of 15 weight parts and the diethylenetriamine melt mixing of 4 weight parts, grind, cross 65 mesh screens;
[0034] (2) Add 13 parts by weight of aliphatic polycarbonate resin, 17 parts by weight of styrene-acrylonitrile resin and 4 parts by weight of silicone leveling agent in the product obtained in step (1), melt and mix;
[0035] (3) Add 37 parts by weight of pigments to the product obtained in step (2) (the weight ratio of chrome green, molybdenum chrome red and carbon black is 1:0.8:2), grind after stirring, and cross a 65-mesh sieve to obtain a coating A1.
Embodiment 2
[0037] (1) Diethylaminopropylamine melt mixing and grinding of the glycidylamine type epoxy resin of 2 parts by weight, the acrylic acid modified polyester resin of 15 parts by weight and 5 parts by weight, and cross 50 mesh screens;
[0038] (2) Add 15 parts by weight of aliphatic polycarbonate resin, 18 parts by weight of styrene-acrylonitrile resin and 5 parts by weight of fluorocarbon leveling agent in the product obtained in step (1), melt mixing;
[0039] (3) Add 40 parts by weight of pigments (the weight ratio of chrome green, molybdenum chrome red and carbon black is 1:0.5:2.5) to the product obtained in step (2), grind after stirring, and cross a 50-mesh sieve to obtain a coating A2.
PUM
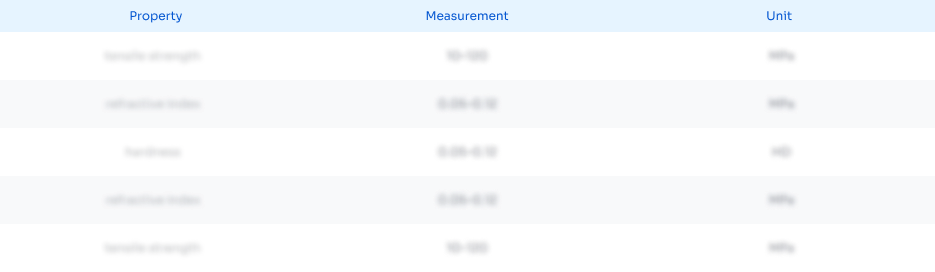
Abstract
Description
Claims
Application Information

- R&D Engineer
- R&D Manager
- IP Professional
- Industry Leading Data Capabilities
- Powerful AI technology
- Patent DNA Extraction
Browse by: Latest US Patents, China's latest patents, Technical Efficacy Thesaurus, Application Domain, Technology Topic, Popular Technical Reports.
© 2024 PatSnap. All rights reserved.Legal|Privacy policy|Modern Slavery Act Transparency Statement|Sitemap|About US| Contact US: help@patsnap.com