Automated assembly line manufacturing technology of coated copper pipe
A manufacturing process and assembly line technology, which is applied in the direction of manufacturing tools, grinding workpiece supports, grinding drive devices, etc., can solve the problems of high manual grinding cost, low grinding efficiency, and long time consumption, so as to improve efficiency and stability. performance, cost reduction
- Summary
- Abstract
- Description
- Claims
- Application Information
AI Technical Summary
Problems solved by technology
Method used
Image
Examples
Embodiment 1
[0033] refer to Figure 1-7, an automated assembly line manufacturing process for coated copper pipes includes a processing table 1, a sliding plate 2 is horizontally slidably connected to both sides of the processing table 1, and a driving assembly is fixedly installed on the bottom of the sliding plate 2, and the two sliding plates 2 are close to each other The same fixed seat 3 is fixedly installed on one side of the fixed seat 3, and a movable clamping assembly is arranged in the fixed seat 3. The same copper pipe 11 is clamped on the movable clamping assembly, and the top of the processing table 1 is rotated and installed with a rotating sleeve 16. The outer fixed sleeve of the rotating sleeve 16 is provided with a first rotating gear 17, and the top of the processing table 1 is provided with a first groove 21, and the bottom inner wall of the first groove 21 is rotatably connected with a second rotating gear 22, and the first The rotating gear 17 is meshed with the secon...
Embodiment 2
[0035] Further improvement on the basis of the first embodiment: both sides of the processing table 1 are fixedly installed with limiting rods 4, and the sliding plate 2 is provided with limiting holes 5, and the two limiting rods 4 respectively pass through the two limiting holes 5 And it is slidingly connected with the limit hole 5, and the limit rod 4 and the limit hole 5 can be used to keep the sliding plate 2 stable when it moves laterally, so that it can move along a straight line; Drive motor 6, drive gear 7 is fixedly installed on the output shaft of drive motor 6, rack 8 is fixedly installed on both sides of processing table 1, and two drive gears 7 are meshed with two racks 8 respectively, when needed When driving the sliding plate 2 to move longitudinally, start the driving motor 6 at this time, and the driving motor 6 can drive the driving gear 7 to rotate. Under the meshing effect of the driving gear 7 and the rack 8, the sliding plate 2 can be driven to move later...
PUM
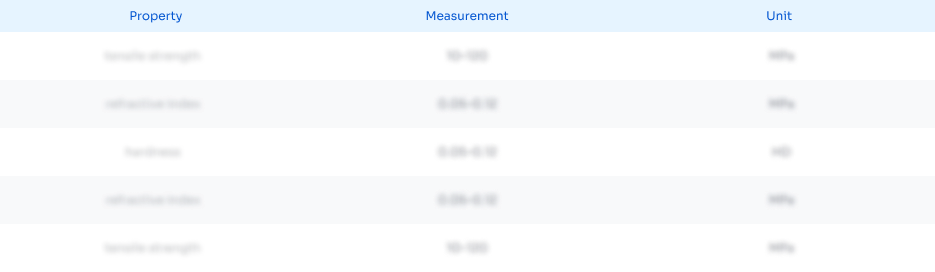
Abstract
Description
Claims
Application Information

- Generate Ideas
- Intellectual Property
- Life Sciences
- Materials
- Tech Scout
- Unparalleled Data Quality
- Higher Quality Content
- 60% Fewer Hallucinations
Browse by: Latest US Patents, China's latest patents, Technical Efficacy Thesaurus, Application Domain, Technology Topic, Popular Technical Reports.
© 2025 PatSnap. All rights reserved.Legal|Privacy policy|Modern Slavery Act Transparency Statement|Sitemap|About US| Contact US: help@patsnap.com