High-strength high-heat-resistance low-scandium sliver added Al-Cu-Mg-series alloy and thermal treatment process thereof
A high heat resistance and alloy technology, applied in the field of low-scandium silver Al-Cu-Mg alloy and its heat treatment process, can solve the problems of expensive addition cost, undisclosed data and technical experience, etc., so as to reduce the preparation cost, excellent The effect of mechanical properties
- Summary
- Abstract
- Description
- Claims
- Application Information
AI Technical Summary
Problems solved by technology
Method used
Image
Examples
Embodiment 1
[0017] An Al-Cu-Mg alloy with high strength, high heat resistance and low scandium silver added, comprising the following steps: (1). Al-4.2Cu-1.5Mg-0.15Sc-0.10Zr-0.12Si- 0.09Ti-0.79Mn-0.3Fe (by mass percentage) alloy ingot was cast, then the ingot was kept at 480°C for 24 hours, and then the temperature was gradually raised to 495°C with the furnace at a heating rate of 5°C / hour, and kept at 12 hours. (2). The processed samples were stored at room temperature for 2 weeks, then aged at 175°C for 12 hours, and air-cooled after taking out the samples.
Embodiment 2
[0019] An Al-Cu-Mg alloy with high strength, high heat resistance and low scandium silver added, comprising the following steps: (1). Al-3.8Cu-1.0Mg-0.16Sc-0.13Zr-0.02Si- 0.02Ti-0.34Mn-0.05Fe (by mass percentage) alloy ingot was cast, then the ingot was kept at 480°C for 24 hours, and then the temperature was gradually raised to 485°C with the furnace at a heating rate of 5°C / hour, and kept at 12 hours. Immediately after the sample was taken out, it was hot-extruded into a 10mm bar, and then air-cooled; (3). The bar in step (2) was homogenized twice at 515° C., kept for 12 hours, and then quenched in warm water. (4). The processed samples were stored at room temperature for 2 weeks, then aged at 175°C for 12 hours, and air-cooled after taking out the samples.
Embodiment 3
[0021] An Al-Cu-Mg alloy with high strength, high heat resistance and low scandium silver added, comprising the following steps: (1). Al-6.8Cu-0.89Mg-0.05Sc-0.20Zr-0.06Si- 0.05Ti-0.88Mn-0.30Fe-0.18Ag (in terms of mass percentage) alloy ingot casting, then the ingot was kept at 485°C for 24 hours, and then the temperature was gradually raised to 515°C with the furnace, the heating rate was 5°C / hour, and the heat preservation time was 24 hours. Hour. Quench the sample in warm water immediately after taking it out; (2). The sample that has been processed in step (1) is parked at room temperature for 2 weeks, then aged at 175° C. for 8 hours, and air-cooled after taking out the sample.
PUM
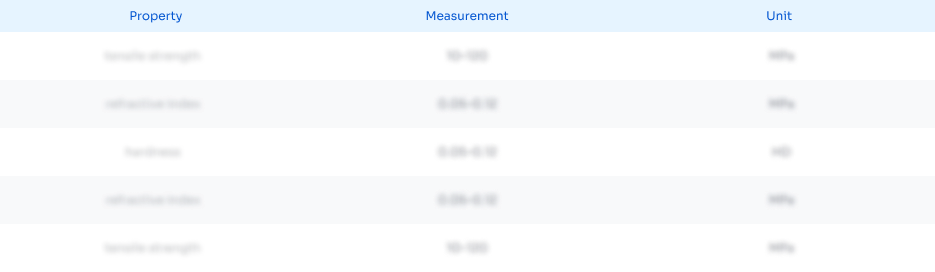
Abstract
Description
Claims
Application Information

- R&D Engineer
- R&D Manager
- IP Professional
- Industry Leading Data Capabilities
- Powerful AI technology
- Patent DNA Extraction
Browse by: Latest US Patents, China's latest patents, Technical Efficacy Thesaurus, Application Domain, Technology Topic, Popular Technical Reports.
© 2024 PatSnap. All rights reserved.Legal|Privacy policy|Modern Slavery Act Transparency Statement|Sitemap|About US| Contact US: help@patsnap.com