High-speed wire mill on-line accurate centering system and method
A high-speed wire rod and rolling mill technology, applied in the direction of guiding/positioning/alignment devices, etc., can solve the problem of being unable to quantitatively provide the centering accuracy of each stand, so as to improve the stability and accuracy of detection, improve the level of automation, and improve alignment. effect based on
- Summary
- Abstract
- Description
- Claims
- Application Information
AI Technical Summary
Problems solved by technology
Method used
Image
Examples
Embodiment 1
[0060] Such as figure 2 As shown, the industrial camera 3 uses a CCD industrial camera, the data processing module 4 uses an industrial computer, and its own display is used as the display module 5. The rolling mill group has seven stands 11, 12, 13, 14, 15, 16, and 17 for continuous rolling. Hole pattern 7 adopts the "round-ellipse-round" series.
[0061] (1) The calibration part is as follows:
[0062] A) Industrial camera adjustment
[0063] Turn on the laser 2 at the exit of the rolling mill, the laser 6 passes through the holes 7 of each rack and then falls into the lens of the industrial camera 3. Adjust the position of the industrial camera 3 so that the center of the light spot is at the center of the detection window. At this time, record the center position of the light spot (X 0 = 800, Y 0 =600), which is the center of alignment. Record the spot diameter as the original diameter D 0 = 20. Adjust the angle of the industrial camera 3 so that only the light spot can be se...
Embodiment 2
[0105] Such as Image 6 As shown, the industrial camera 3 uses a CCD industrial camera, the data processing module 4 uses an industrial computer, and its own display is used as the display module 5. The rolling mill group has five racks 11, 12, 13, 14, 15 for continuous rolling, and the pass type 7 uses "Ellipse-Circle-Ellipse" series.
[0106] (1) The calibration part is as follows:
[0107] A) Industrial camera adjustment
[0108] Turn on the laser 2 at the exit of the rolling mill, the laser 6 passes through the holes 7 of each rack 11-15 and then falls into the lens of the industrial camera 3. Adjust the position of the industrial camera 3 so that the center of the light spot is at the center of the detection window. At this time, record the center position of the light spot (X 0 = 800, Y 0 =600), which is the center of alignment. Record the spot diameter as the original diameter D 0 = 30. Adjust the angle of the industrial camera 3 so that only the light spot can be seen in t...
PUM
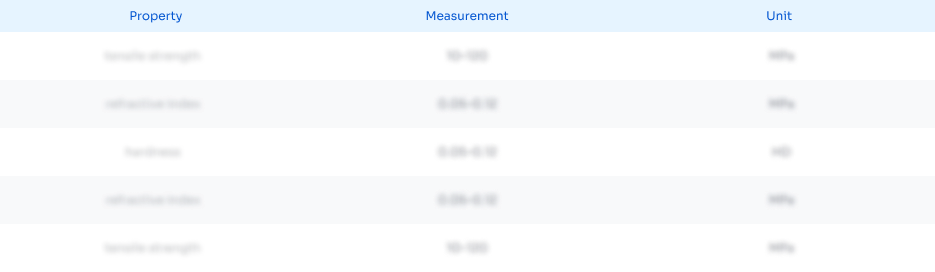
Abstract
Description
Claims
Application Information

- Generate Ideas
- Intellectual Property
- Life Sciences
- Materials
- Tech Scout
- Unparalleled Data Quality
- Higher Quality Content
- 60% Fewer Hallucinations
Browse by: Latest US Patents, China's latest patents, Technical Efficacy Thesaurus, Application Domain, Technology Topic, Popular Technical Reports.
© 2025 PatSnap. All rights reserved.Legal|Privacy policy|Modern Slavery Act Transparency Statement|Sitemap|About US| Contact US: help@patsnap.com