Low-cost environment-friendly method for preparing epoxidized silicone rubber
A silicone rubber and epoxidation technology, which is applied in the field of low-cost and environmentally friendly preparation of epoxidized silicone rubber, can solve the problems of low glass transition temperature, and the preparation method is not suitable for industrial scale-up use, so as to shorten the time and reduce the post-processing time , The effect of simple production process
- Summary
- Abstract
- Description
- Claims
- Application Information
AI Technical Summary
Problems solved by technology
Method used
Image
Examples
Embodiment 1
[0054] Take 1525g of octamethylcyclotetrasiloxane and 443g of tetramethyltetravinylcyclotetrasiloxane and put them into a 5L strong dispersing reaction kettle, keep the vacuum degree below -0.1MPa at 45°C, and remove water under a small amount of nitrogen gas for 1 After 1 hour, 9.77 g of catalyst and 1.62 g of end-capping agent were added, and water was removed at -0.1 MPa at 45° C. under a small amount of nitrogen for 1.5 hours. After removing water and returning to normal pressure, set the temperature to 110° C., and react for 3 hours under nitrogen atmosphere. After the reaction, set the temperature at 170°C, and at the same time start vacuuming at -0.1MPa under a small amount of nitrogen to remove low molecules, and the time for removing low molecules is 6h. After removal of low molecules, a high vinyl silicone rubber with a vinyl segment molar content of 20% is obtained.
[0055] Take 3g of high-vinyl silicone rubber with a vinyl content of 20% and a 250ml three-necked fl...
Embodiment 2
[0062] Take 1525g of octamethylcyclotetrasiloxane and 443g of tetramethyltetravinylcyclotetrasiloxane and put them into a 5L strong dispersing reaction kettle, keep the vacuum degree below -0.1MPa at 45°C, and remove water under a small amount of nitrogen gas for 1 hours, then add 9.77g of catalyst and 1.62g of end-capping agent, and remove water at -0.1MPa at 45°C for 1.5 hours under a small amount of nitrogen. After removing water and returning to normal pressure, set the temperature to 110° C., and react for 3 hours under nitrogen atmosphere. After the reaction, set the temperature at 170°C, and at the same time start vacuuming at -0.1MPa under a small amount of nitrogen to remove low molecules, and the time for removing low molecules is 6h. After removal of low molecules, a high vinyl silicone rubber with a vinyl segment molar content of 20% is obtained.
[0063] Take 3g of high-vinyl silicone rubber with a vinyl content of 20% and a 250ml three-necked flask, add 100g of ...
Embodiment 3
[0065] Take 1335g of octamethylcyclotetrasiloxane and 662.4g of tetramethyltetravinylcyclotetrasiloxane and put them into a 5L strong dispersing reaction kettle, keep the vacuum degree below -0.1MPa at 45°C, and remove water under a small amount of nitrogen gas After 1 hour, 9.74 g of catalyst and 1.60 g of end-capping agent were added, and water was removed at -0.1 MPa at 45° C. under a small amount of nitrogen for 1.5 hours. After removing water and returning to normal pressure, set the temperature to 110° C., and react for 3 hours under nitrogen atmosphere. After the reaction, set the temperature at 170°C, and at the same time start vacuuming at -0.1MPa under a small amount of nitrogen to remove low molecules, and the time for removing low molecules is 6h. After removal of low molecules, a high vinyl silicone rubber with a vinyl segment molar content of 30% is obtained.
[0066] Take 3g of high-vinyl silicone rubber with a vinyl content of 30% and a 250ml three-necked flas...
PUM
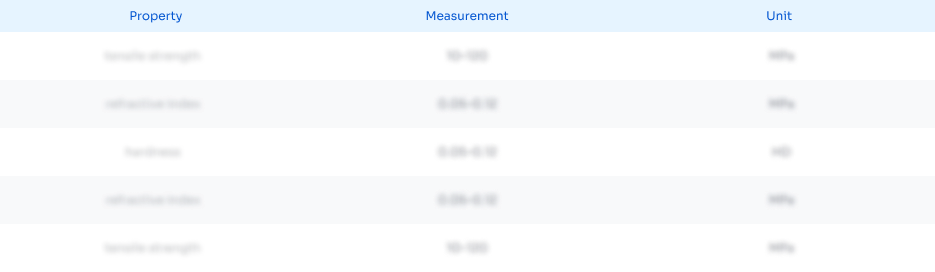
Abstract
Description
Claims
Application Information

- R&D
- Intellectual Property
- Life Sciences
- Materials
- Tech Scout
- Unparalleled Data Quality
- Higher Quality Content
- 60% Fewer Hallucinations
Browse by: Latest US Patents, China's latest patents, Technical Efficacy Thesaurus, Application Domain, Technology Topic, Popular Technical Reports.
© 2025 PatSnap. All rights reserved.Legal|Privacy policy|Modern Slavery Act Transparency Statement|Sitemap|About US| Contact US: help@patsnap.com