Method for continuously producing polypropylene carbonate by preheating liquid phase method in channelization manner
A polypropylene carbonate and pipeline technology is applied in the field of preheating liquid phase method pipeline continuous production of polypropylene carbonate, which can solve the problems of increasing the viscosity of the copolymerization reaction system, the production cost and the low cost of catalyst residues, and the cyclic carbonic acid. The problem of increasing ester ratio, etc., can improve the mass transfer and heat transfer ability and effect, avoid poor selectivity and activity, and increase the content of carbonate units.
- Summary
- Abstract
- Description
- Claims
- Application Information
AI Technical Summary
Problems solved by technology
Method used
Image
Examples
Embodiment 1
[0040] A method for the continuous production of polypropylene carbonate in a pipeline by a preheating liquid phase method,
[0041] The method comprises the steps of:
[0042] (1) After the raw materials including propylene oxide and catalyst are mixed uniformly in the premix tank in a certain proportion, they are pumped into the pipeline reactor, and the pipeline reactor includes a reaction section group and a cooling section group, and the reaction section group placed at the inlet end of the piped reactor, and the cooling segment set is placed at the outlet end of the piped reactor;
[0043](2) After carbon dioxide is preheated to 40-150°C, it is pumped in from the inlet of the pipeline reactor, so that the pipeline reactor is pressurized to 1-15MPa;
[0044] (3) The raw materials are mixed into a reaction solution in a pipelined reactor, heated to 70-150° C., so that in the presence of the catalyst, propylene oxide and carbon dioxide are contacted in the pipelined reacto...
Embodiment 2
[0076] Example 2 refers to Experimental Example 1. The difference is that in Example 2, after carbon dioxide is preheated to 70-120°C, specifically to about 100°C, the carbon dioxide is transferred from the reaction section group to the pipelined reactor. The purpose of adding the carbon dioxide is to make the reaction section group have enough carbon dioxide by adding carbon dioxide, and the raw materials in the reaction section group are mixed evenly, so as to avoid the occurrence of dead zones, thereby avoiding the local enrichment of propylene oxide, and also through Carbon dioxide is added to control the polymerization temperature of the group of reaction zones.
Embodiment 3
[0086] Example 3 refers to Experimental Example 1. The difference is that in Example 3, after the propylene oxide is preheated to 40-120°C, specifically to about 90°C, the reaction section group is injected into the pipeline reactor The purpose of adding propylene oxide is to control the concentration of propylene oxide in the reaction section group within the target range by adding propylene oxide, and to mix the raw materials in the reaction section group evenly, and to control the concentration of propylene oxide by adding propylene oxide. The polymerization reaction temperature of the reaction section group.
PUM
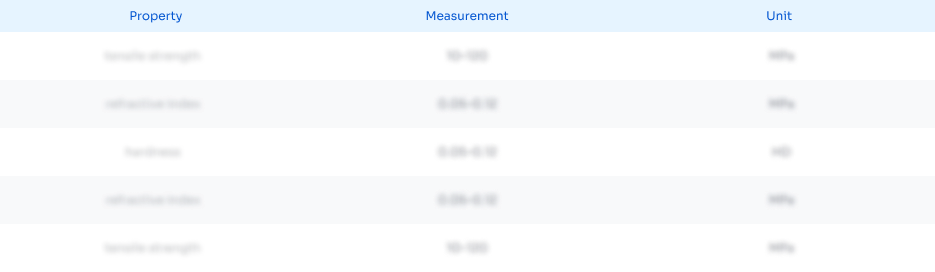
Abstract
Description
Claims
Application Information

- R&D
- Intellectual Property
- Life Sciences
- Materials
- Tech Scout
- Unparalleled Data Quality
- Higher Quality Content
- 60% Fewer Hallucinations
Browse by: Latest US Patents, China's latest patents, Technical Efficacy Thesaurus, Application Domain, Technology Topic, Popular Technical Reports.
© 2025 PatSnap. All rights reserved.Legal|Privacy policy|Modern Slavery Act Transparency Statement|Sitemap|About US| Contact US: help@patsnap.com