A kind of technology and application of separating and recovering zinc-magnesium sulfate double salt from sulfate solution
A technology for separation and recovery of sulfate, applied in the direction of zinc compounds, chemical instruments and methods, inorganic chemistry, etc., can solve the problems of zinc and magnesium losing the value of recycling, and achieve the effect of less reagent consumption, clean and environmentally friendly process
- Summary
- Abstract
- Description
- Claims
- Application Information
AI Technical Summary
Problems solved by technology
Method used
Examples
Embodiment 1
[0020] Get the sulfate solution 10L that chemical plant produces (its solution temperature is 65 ℃, main chemical composition is zinc 130g / L, magnesium 28g / L, other element concentrations are all lower, and sulfuric acid concentration is 0.2g / L in the solution. At first Add this sulfate solution into the pre-cooler, use the crystallization mother liquor with a temperature of -5°C for heat exchange pre-cooling, and cool it to 30°C. Then add the pre-cooled solution into the crystallization reactor. Use a coil heat exchanger Cool down, start stirring, and the stirring speed is 30 rpm. In the first stage, the cooling rate is 0.2°C / min. When cooling to 15°C, the solution starts to become turbid, stop cooling, keep warm and stir for 30min. Then start The second stage cooling, with the cooling rate being 0.5 ℃ / min cooling rate to be cooled to-5 ℃, be incubated and stir 60min.After reaction finishes, adopt centrifugal filter to filter, filter product oven dry and obtain 3500g zinc-magn...
Embodiment 2
[0022] Take 10L of sulfate solution produced by the smelting plant (the temperature of the solution is 40°C, the main chemical components are zinc 40g / L, magnesium 26g / L, sulfuric acid 180g / L and other element concentrations are low). Firstly, put the sulfate solution into the pre-cooler, use the crystallization mother liquor with a temperature of -10°C for heat exchange and pre-cooling, and cool to 10°C. The pre-cooled solution is then added to the crystallization reactor. Use a coil heat exchanger to cool down, start stirring, and the stirring speed is 60 rpm. In the first stage, the cooling rate was 0.3 °C / min. When the temperature was lowered to 0 °C, the solution began to become cloudy, so the cooling was stopped, and the temperature was kept and stirred for 20 min. Then start the second stage of cooling, and lower the temperature to -10°C at a cooling rate of 0.8°C / min, keep warm and stir for 40min. After reaction finishes, adopt centrifugal filter to filter, and filte...
Embodiment 3
[0024] Take 10L of sulfate solution produced in the printing and dyeing industry (the temperature of the solution is 25°C, the main chemical components are zinc 75g / L, magnesium 87g / L, and the concentration of sulfuric acid is 75g / L). First, add the sulfate solution into the pre-cooler, use crystallization mother liquor at 0°C for heat exchange pre-cooling, and cool to 15°C. The pre-cooled solution is then added to the crystallization reactor. Use a coil heat exchanger to cool down, start stirring, and the stirring speed is 100 rpm. In the first stage, the cooling rate was 0.5°C / min. When the temperature was lowered to 10°C, the solution began to become turbid, so the cooling was stopped, and the temperature was kept and stirred for 30 minutes. Then start the second stage of cooling, and lower the temperature to 0 °C at a cooling rate of 1 °C / min, keep warm and stir for 60 min. After reaction finishes, adopt centrifugal filter to filter, and filter product oven dry obtains 4...
PUM
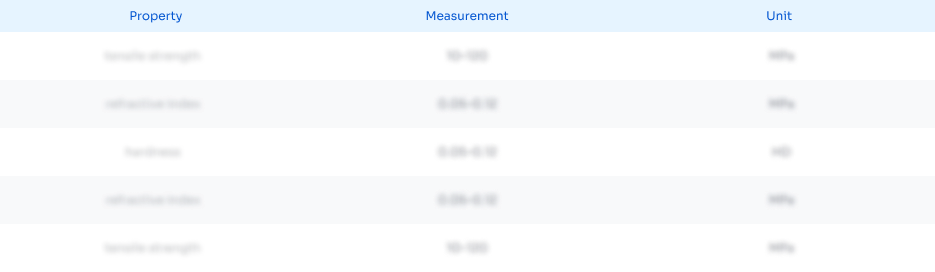
Abstract
Description
Claims
Application Information

- R&D
- Intellectual Property
- Life Sciences
- Materials
- Tech Scout
- Unparalleled Data Quality
- Higher Quality Content
- 60% Fewer Hallucinations
Browse by: Latest US Patents, China's latest patents, Technical Efficacy Thesaurus, Application Domain, Technology Topic, Popular Technical Reports.
© 2025 PatSnap. All rights reserved.Legal|Privacy policy|Modern Slavery Act Transparency Statement|Sitemap|About US| Contact US: help@patsnap.com