An anti-collision support structure for dock lifting equipment
A lifting equipment and support structure technology, which is applied to the bottom support structure, crane, mechanical equipment, etc., can solve the problems of buffering, guiding and fixing of the anti-collision structure, affecting the stability of the lifting equipment, and large shaking of the lifting equipment. The effect of reducing shaking, avoiding damage, and good protective treatment
- Summary
- Abstract
- Description
- Claims
- Application Information
AI Technical Summary
Problems solved by technology
Method used
Image
Examples
Embodiment 1
[0028] see Figure 1-5, an anti-collision support structure for dock lifting equipment, including a main beam frame 1, support columns 2 are fixedly installed on both sides of the bottom end of the main beam frame 1, and a mounting plate 4 is fixedly connected to the bottom end of the support column 2 , the middle part of the support column 2 is fixedly connected with the first connecting cylinder 3, one end of the first connecting cylinder 3 is slidably connected with the mounting column 5, the inner wall of the first connecting cylinder 3 is slidably connected with the sliding plate 6, and one end of the mounting column 5 is fixedly connected with the The middle part of one end of the sliding plate 6, one end of the sliding plate 6 is fixedly connected with the second spring 12, and the second spring 12 is positioned at the side wall of the mounting column 5, the other end of the mounting column 5 is fixedly connected with the mounting bracket 7, and the supporting column 2 ...
Embodiment 2
[0031] see Figure 1-5 , on the basis of Embodiment 1, a further improvement has been made: a fixed plate 8 is fixedly connected between the main beam frame 1 and the mounting plate 4, and one end of the fixed plate 8 is fixedly connected with a mounting tube 9, and the mounting tube 9 is slidably connected with a second A sliding column 10, and the first sliding column 10 is supported in the middle part of one end of the sliding plate 6; one end of the sliding plate 6 is fixedly equipped with a first spring 11, and the first spring 11 is positioned at the side wall of the first sliding column 10; the supporting column One end of 2 is fixedly connected with a second connecting cylinder 13, a second sliding column 16 is slidably connected between one end of the second connecting cylinder 13 and one end of the third connecting cylinder 15, and a first limit sliding column is slidably connected inside the second connecting cylinder 13. Disk 17, one end of the first limiting slidi...
Embodiment 3
[0034] see Figure 1-5 , made a further improvement on the basis of Embodiment 1: one end of the mounting frame 7 is fixedly installed with a protective pad 22, and one end of the protective pad 22 is fixedly connected with several vibration-damping rubber rings 23; between the two vibration-damping rubber rings 23 Several connection blocks 24 are fixedly connected, and the connection blocks 24 are located inside the protective pad 22 .
[0035] In this embodiment, a protective pad 22 is provided at one end of the mounting bracket 7, and then a plurality of vibration-damping rubber rings 23 are fixedly connected to one end of the protective pad 22, and several vibration-damping rubber rings 23 are connected together by a connecting block 24, So that the goods can be better supported.
PUM
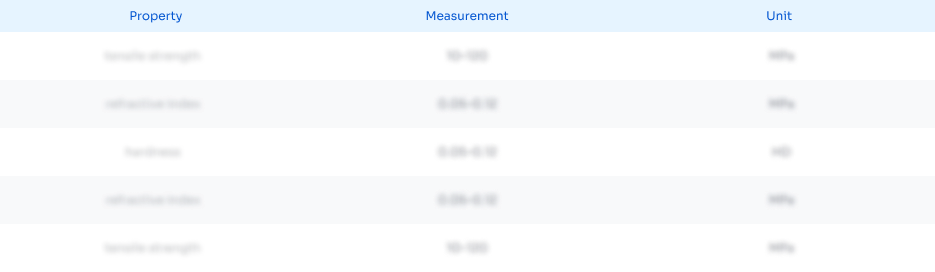
Abstract
Description
Claims
Application Information

- R&D
- Intellectual Property
- Life Sciences
- Materials
- Tech Scout
- Unparalleled Data Quality
- Higher Quality Content
- 60% Fewer Hallucinations
Browse by: Latest US Patents, China's latest patents, Technical Efficacy Thesaurus, Application Domain, Technology Topic, Popular Technical Reports.
© 2025 PatSnap. All rights reserved.Legal|Privacy policy|Modern Slavery Act Transparency Statement|Sitemap|About US| Contact US: help@patsnap.com