Optical alignment debugging process and optical tool setting device of clamping diamond micro milling cutter
An optical alignment and diamond technology, applied in workpiece clamping devices, manufacturing tools, hand-held tools, etc., can solve problems that restrict the development of ultra-precision micro-milling technology, assembly accuracy errors, etc., to improve the quality of the processed surface and achieve precise Assembly, reduce overcut effect
- Summary
- Abstract
- Description
- Claims
- Application Information
AI Technical Summary
Problems solved by technology
Method used
Image
Examples
Embodiment 1
[0018] For diamond micromilling cutters assembled with high precision, see figure 1 , present embodiment 1 provides a kind of optical alignment debugging process of clamping type diamond micro-milling cutter, comprises the following steps: step S1, debugging CCD digital camera group; on a precision adjustment platform; step S3, within the imaging field of view of the CCD digital camera group, adjust the corresponding precision adjustment platform so that the handle is positioned directly below the milling blade; and step S4, clamp the milling blade in a clamping manner Tightly fastened to the handle.
[0019] Optionally, the tool holder is a carbide tool holder, and the milling blade is a diamond milling blade.
[0020] Optionally, the clamping method is, for example but not limited to, a combination of a pressing plate and a screw.
[0021] Optionally, the debugging CCD digital camera group includes: step S11, setting corresponding CCD digital cameras in the horizontal dire...
Embodiment 2
[0029] On the basis of embodiment 1, see figure 2 , the present embodiment 2 provides a clamping type diamond micro-milling cutter optical tool setting device, including: CCD digital camera group (as long as the tool handle debugging assembly 1, milling blade debugging assembly 2, tool handle 3, milling blade 4 Just within the imaging field of view of the CCD digital camera group, not shown in the figure), tool handle debugging component 1, milling blade debugging component 2; within the imaging field of view of the CCD digital camera group, adjust the tool handle debugging component 1, The milling blade debugging assembly 2 makes the tool handle 3 directly below the milling blade 4, so that the milling blade 4 is clamped and fixed on the tool handle 3 by clamping.
[0030] Optionally, the CCD digital camera group includes CCD digital cameras respectively arranged in the horizontal direction and the vertical direction, that is, a horizontal CCD digital camera and a vertical C...
PUM
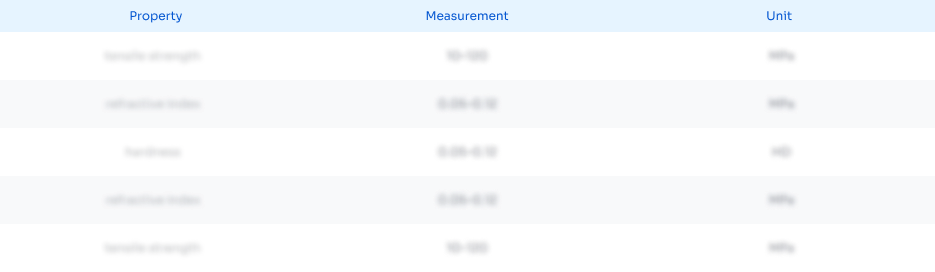
Abstract
Description
Claims
Application Information

- Generate Ideas
- Intellectual Property
- Life Sciences
- Materials
- Tech Scout
- Unparalleled Data Quality
- Higher Quality Content
- 60% Fewer Hallucinations
Browse by: Latest US Patents, China's latest patents, Technical Efficacy Thesaurus, Application Domain, Technology Topic, Popular Technical Reports.
© 2025 PatSnap. All rights reserved.Legal|Privacy policy|Modern Slavery Act Transparency Statement|Sitemap|About US| Contact US: help@patsnap.com