Precision treatment process after molding of alloy shell of electric motor
An electric motor and processing technology, applied in metal processing equipment, manufacturing tools, grinding workpiece supports, etc., can solve the problems of residual debris, reduced production efficiency, uneven surface of alloy shell, etc., to ensure precision, improve The effect of processing efficiency and quality improvement
- Summary
- Abstract
- Description
- Claims
- Application Information
AI Technical Summary
Problems solved by technology
Method used
Image
Examples
Embodiment Construction
[0028] In order to make the technical means, creative features, goals and effects achieved by the present invention easy to understand, the present invention will be further described below in conjunction with specific illustrations. It should be noted that, in the case of no conflict, the embodiments in the present application and the features in the embodiments can be combined with each other.
[0029] Such as Figure 1 to Figure 6 As shown, a precision treatment process for forming an electric motor alloy shell is mainly completed by a precision treatment device after forming an electric motor alloy shell. The precision treatment device after forming an electric motor alloy shell includes a bracket 1. The fixed base 6 is provided with chute 61 symmetrically on the fixed base 6, and a slider 62 is inserted in the chute 61, and the top of the slider 62 is fixedly connected with the bottom of the bracket 1, and the fixed base 6 is used for fixing , the chute 61 cooperates wit...
PUM
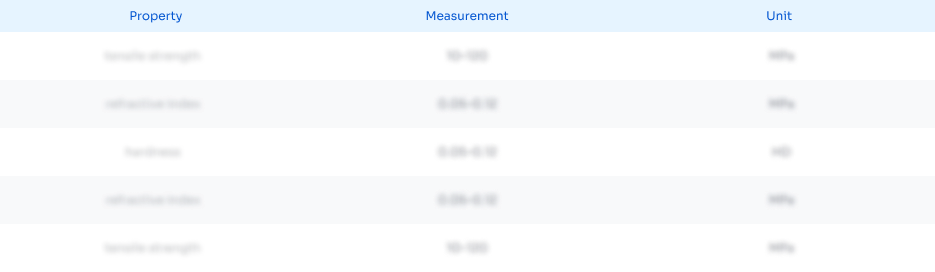
Abstract
Description
Claims
Application Information

- Generate Ideas
- Intellectual Property
- Life Sciences
- Materials
- Tech Scout
- Unparalleled Data Quality
- Higher Quality Content
- 60% Fewer Hallucinations
Browse by: Latest US Patents, China's latest patents, Technical Efficacy Thesaurus, Application Domain, Technology Topic, Popular Technical Reports.
© 2025 PatSnap. All rights reserved.Legal|Privacy policy|Modern Slavery Act Transparency Statement|Sitemap|About US| Contact US: help@patsnap.com