Hot-rolling technology method for improving surface quality of car outer plate
A technology of surface quality and process method, applied in the field of hot rolling, can solve the problems affecting the performance of the finished product, edge defects, regional mixed crystals, etc., and achieve the effect of excellent deep drawing performance, elimination of edge defects, and elimination of stamping streak defects.
- Summary
- Abstract
- Description
- Claims
- Application Information
AI Technical Summary
Problems solved by technology
Method used
Image
Examples
Embodiment Construction
[0029] In the analysis and research of the stamping streak defects that occurred during the application of IF steel, detailed tests, comparisons and analyzes were carried out on each process point of the hot rolling process, and it was found that the main process parameters and equipment conditions of hot rolling have a significant impact on the cold rolled finished product. The influence of surface quality plays an important role, and the influence of high final rolling temperature of hot rolling on the microstructure of finished strip steel and the improvement of streak defects to a certain extent has also been studied in detail. At the same time, by benchmarking the IF steel process of the advanced production line and the consistent management of the surface quality of the outer panel of the automobile, the parameters of the hot rolling process of the outer panel of the automobile were optimized, and the final rolling temperature was increased from the original target of 900°...
PUM
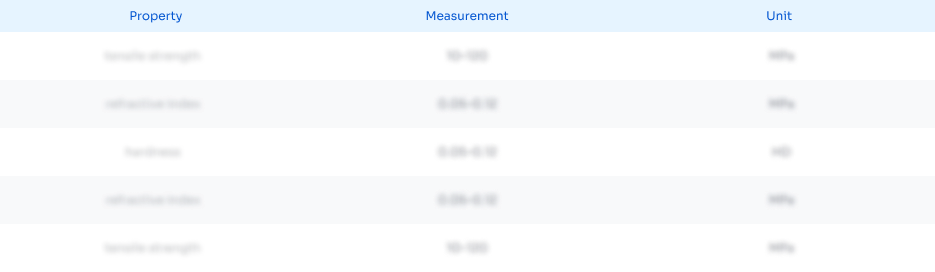
Abstract
Description
Claims
Application Information

- R&D
- Intellectual Property
- Life Sciences
- Materials
- Tech Scout
- Unparalleled Data Quality
- Higher Quality Content
- 60% Fewer Hallucinations
Browse by: Latest US Patents, China's latest patents, Technical Efficacy Thesaurus, Application Domain, Technology Topic, Popular Technical Reports.
© 2025 PatSnap. All rights reserved.Legal|Privacy policy|Modern Slavery Act Transparency Statement|Sitemap|About US| Contact US: help@patsnap.com