Short-process high-recycling-rate smelting method for chalcocite
A technology with high recovery rate and smelting method, applied in crucible furnaces, electric furnaces, rotary drum furnaces, etc., can solve the problems of low copper recovery rate, high smelting cost, and long process, so as to improve copper recovery rate, reduce processing cost, Yield reduction effect
- Summary
- Abstract
- Description
- Claims
- Application Information
AI Technical Summary
Problems solved by technology
Method used
Examples
Embodiment 1
[0019] Chalcocite assay composition: Cu: 62%, Fe: 2%, SiO 2 : 8%, S: 14%; copper matte assay composition Cu: 72%, Fe: 3%, S: 20%.
[0020] Add chalcocite to the silo equipped with a quantitative feeder first, and adjust the addition of chalcocite and copper matte to the converting furnace per hour according to the furnace temperature, oxygen ventilation rate, slag type and other parameters of the converting furnace quantity. In the present embodiment, the addition of chalcocite to the converting furnace is 8t per hour, and the addition of hot copper matte to the converting furnace is 14t per hour. In the present embodiment, Fe: SiO 2 is 0.91, no need to add slagging agent quartz ore; chalcocite is continuously and uniformly added to the converting furnace through the belt, and the copper matte is intermittently added to the converting furnace through the chute in the form of full heat from the copper matte mouth of the melting furnace For blowing. The mixed oxygen concentra...
Embodiment 2
[0022] Chalcocite assay composition: Cu: 50%, Fe: 1.8%, SiO 2 : 10%, S: 13%; copper matte assay composition Cu: 70%, Fe: 5%, S: 20.2%.
[0023] Add chalcocite to the silo equipped with a quantitative feeder first, and adjust the addition of chalcocite and copper matte to the converting furnace per hour according to the furnace temperature, oxygen ventilation rate, slag type and other parameters of the converting furnace quantity. In the present embodiment, the addition amount of chalcocite to the converting furnace is 6t per hour, and the addition amount of cold copper matte to the converting furnace is 19t per hour. In the present embodiment, Fe: SiO 2 is 3.09, exceeding the range of 0.8 to 1.2, so 0.5t of quartz stone is added to the converting furnace per hour; chalcocite is continuously and uniformly added to the converting furnace through a belt for blowing. All the added copper mattes are continuously fed into the converting furnace through a belt in a cold state. The...
Embodiment 3
[0025] Chalcocite assay composition: Cu: 40%, Fe: 1.5%, SiO 2 : 14%, S: 13%; copper matte assay composition Cu: 70%, Fe: 5%, S: 20.2%.
[0026] Add chalcocite to the silo equipped with a quantitative feeder first, and adjust the addition of chalcocite and copper matte to the converting furnace per hour according to the furnace temperature, oxygen ventilation rate, slag type and other parameters of the converting furnace quantity. In the present embodiment, the addition amount of chalcocite to the converting furnace is 7t per hour, and the addition amount of hot copper matte to the converting furnace is 20t per hour. In the present embodiment, Fe: SiO 2 It is 1.13, no need to add slagging agent quartz stone; chalcocite is continuously and uniformly added to the converting furnace through the belt, and copper matte is intermittently added to the converting furnace through the chute in the form of full heat from the copper matte mouth of the melting furnace For blowing. The mi...
PUM
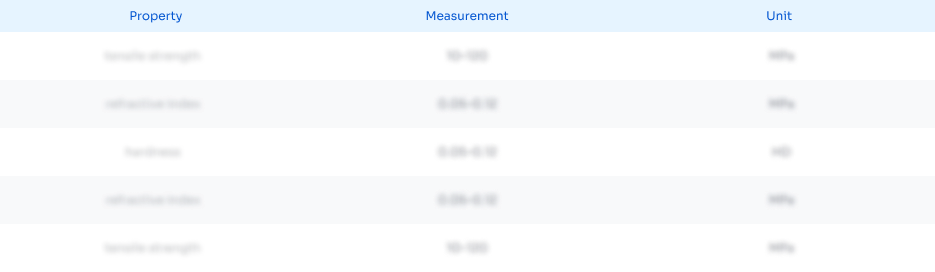
Abstract
Description
Claims
Application Information

- Generate Ideas
- Intellectual Property
- Life Sciences
- Materials
- Tech Scout
- Unparalleled Data Quality
- Higher Quality Content
- 60% Fewer Hallucinations
Browse by: Latest US Patents, China's latest patents, Technical Efficacy Thesaurus, Application Domain, Technology Topic, Popular Technical Reports.
© 2025 PatSnap. All rights reserved.Legal|Privacy policy|Modern Slavery Act Transparency Statement|Sitemap|About US| Contact US: help@patsnap.com