Method for quickly preparing peracetic acid through continuous flow
A peracetic acid and fast technology, which is applied in the preparation of peroxygen compounds, chemical instruments and methods, and the preparation of organic compounds, can solve the problems of large equipment investment, high safety risks, and high manufacturing costs, and achieve fast mass and heat transfer , improve reaction efficiency, and occupy a small area of equipment
- Summary
- Abstract
- Description
- Claims
- Application Information
AI Technical Summary
Problems solved by technology
Method used
Image
Examples
Embodiment 1
[0032] One enhanced mixed microchannel module was selected as the pre-mixed preheating module, six enhanced mixed microchannel modules were used as the reaction module, and one enhanced mixed microchannel module was selected as the cooling module to form a continuous flow microchannel reaction system according to the reaction process.
[0033] The microchannel structure of each module is an enhanced mixed channel heart-shaped structure, and the channel diameter is 0.5-10mm; as for the number of modules, it is mainly to ensure that there is enough residence time.
[0034] The heat transfer medium of the preheating module and the reaction module is heat transfer oil, and the heat transfer medium of the cooling module is ethylene glycol / ethanol. According to the forced heat transfer principle of the microchannel reactor, only two temperature measuring points are set at the feed inlet and outlet of the reactor. Before the reaction, the microchannel reaction system and connecting p...
Embodiment 2
[0040] Use the microchannel reactor identical with embodiment 1, and according to same connection mode and control method. In this example, the reaction conditions were changed.
[0041] Step (1): According to the 1.1:1 molar ratio of acetic acid and hydrogen peroxide, mix acetic acid and 70wt% hydrogen peroxide, then add 0.5wt% mass fraction of 98% concentrated sulfuric acid and 0.3wt% of the total mass of the reaction solution respectively The ethylenediaminetetraacetic acid was mixed evenly, and the reaction liquid mixture was continuously and stably pumped into the microchannel reaction system through the plunger pump, and the temperature of the heat exchanger of the preheating module was set at 80°C.
[0042] Step (2): After the step (1) is preheated, the reaction mixture continuously enters the microchannel reaction module, the temperature of the heat exchanger of the reaction module is set to 80°C, the back pressure valve is adjusted to maintain the pressure of the reac...
Embodiment 3
[0046] Use the microchannel reactor identical with embodiment 1, and according to same connection mode and control method. In this example, the reaction conditions were changed.
[0047] Step (1): According to the 4:1 molar ratio of acetic acid and hydrogen peroxide, mix acetic acid and 30wt% hydrogen peroxide, then add 5wt% methanesulfonic acid and 0.5wt% sodium phosphate of the total mass of the reaction solution and mix Evenly, continuously and stably pump the reaction solution mixture into the microchannel reaction system through the plunger pump, and set the temperature of the heat exchanger of the preheating module to 148°C.
[0048] Step (2): After preheating in step (1), the reaction mixture continuously enters the microchannel reaction module. Set the temperature of the heat exchanger of the reaction module to 148° C., adjust the back pressure valve to maintain the pressure of the reaction system at 1.3 MPa, and set the column The plug pump flow was such that the rea...
PUM
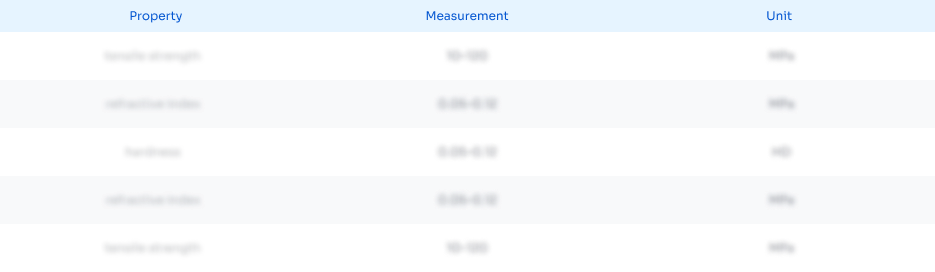
Abstract
Description
Claims
Application Information

- R&D
- Intellectual Property
- Life Sciences
- Materials
- Tech Scout
- Unparalleled Data Quality
- Higher Quality Content
- 60% Fewer Hallucinations
Browse by: Latest US Patents, China's latest patents, Technical Efficacy Thesaurus, Application Domain, Technology Topic, Popular Technical Reports.
© 2025 PatSnap. All rights reserved.Legal|Privacy policy|Modern Slavery Act Transparency Statement|Sitemap|About US| Contact US: help@patsnap.com