Backing plate positioning mechanism for BL automatic assembly production line
An automatic assembly and production line technology, applied in metal processing, metal processing equipment, manufacturing tools, etc., can solve the problems of assembly material loss, personnel waste, and delay in finding problems, reducing defect rate, reducing direct impact, The effect of reducing the amount of foreign matter generated
- Summary
- Abstract
- Description
- Claims
- Application Information
AI Technical Summary
Problems solved by technology
Method used
Image
Examples
Embodiment 1
[0039] In order to reduce the defect occurrence rate of the automatic assembly line in the assembly process, the present invention provides a backboard horizontal positioning structure for the BL automatic assembly line. 200 has been improved in turn, which can not only reduce the impact force of the back plate and the longitudinal positioning mechanism, but also overcome the friction force between the back plate and the lateral positioning mechanism, so as to solve the problem of high foreign matter defect rate of BL produced by the automatic assembly line and the displacement of the film material. The problem of high assembly failure rate.
[0040] Wherein, the backplane positioning mechanism includes a horizontal positioning assembly 200 and a vertical positioning assembly 100 arranged vertically, wherein the vertical positioning mechanism is arranged along the longitudinal direction of the assembly line.
[0041] For portrait positioning component 100:
[0042] see figur...
Embodiment 2
[0066] In another embodiment, two buffer bodies 104 are arranged on the front positioning structure 102 , the two buffer bodies 104 are symmetrically arranged on the positioning structure, and each buffer body 104 corresponds to one buffer groove 103 .
Embodiment 3
[0068] In one embodiment, a buffer body 104 is provided on the front positioning structure 102 , and the buffer body 104 includes two buffer springs 105 , and the two buffer springs 105 are symmetrically arranged on the buffer block 106 .
PUM
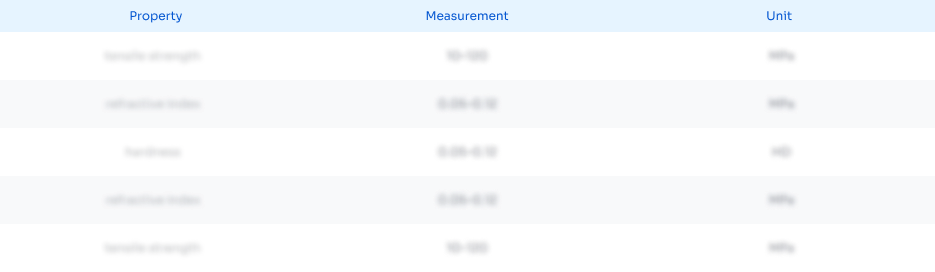
Abstract
Description
Claims
Application Information

- R&D
- Intellectual Property
- Life Sciences
- Materials
- Tech Scout
- Unparalleled Data Quality
- Higher Quality Content
- 60% Fewer Hallucinations
Browse by: Latest US Patents, China's latest patents, Technical Efficacy Thesaurus, Application Domain, Technology Topic, Popular Technical Reports.
© 2025 PatSnap. All rights reserved.Legal|Privacy policy|Modern Slavery Act Transparency Statement|Sitemap|About US| Contact US: help@patsnap.com