A treatment method for separating and recovering copper, iron, zinc, nickel and chromium from chromium-containing sludge
A treatment method, separation and recovery technology, applied to the separation and recovery of copper, iron, zinc, chromium from chromium-containing sludge, and the field of nickel, which can solve the problems of cumbersome steps and high requirements for supporting facilities, so as to reduce the content of chromium , the effect of reducing production
- Summary
- Abstract
- Description
- Claims
- Application Information
AI Technical Summary
Problems solved by technology
Method used
Image
Examples
Embodiment 1
[0036] The chromium-containing sludge in a factory area contains 20% chromium, 10% zinc, 5% Cu, 1% Fe, and 1% Ni. Add sulfuric acid to 100g of chromium-containing sludge to dissolve completely, the concentration of acid added is 10%, and the amount of acid added is 400g. After electrolyzing the acid-dissolved solution for 24 hours, the copper in the solution was removed, and the concentration of copper ions in the solution was 37 mg / m 3 , 4.8g copper elemental substance was recovered. And use the extraction method to remove the iron in the solution, the iron ion concentration in the solution is 49mg / m 3 . After back-extracting the iron extract, a solution of ferric iron is obtained, and after reduction with excess reduced iron powder, a ferrous sulfate solution is obtained. Add 10% sodium hydroxide to the solution to adjust the pH value to 9, and filter to obtain sludge and high-salt solution. Add ferrous sulfate to the high-salt solution, adjust the pH value to 11, heat a...
Embodiment 2
[0044] The chromium-containing sludge in a factory area contains 15% chromium, 3% zinc, 6% Cu, 2% Fe and 2% Ni. Add sulfuric acid to 100g of chromium-containing sludge to dissolve completely, the concentration of acid added is 40%, and the amount of acid added is 100g. After electrolyzing the acid-dissolved solution for 24 hours, the copper in the solution was removed, and the concentration of copper ions in the solution was 42mg / m 3 , 5.9g copper elemental substance was recovered. And use the extraction method to remove the iron in the solution, the iron ion concentration in the solution is 21mg / m 3 . After back-extracting the iron extract, a solution of ferric iron is obtained, and after reduction with excess reduced iron powder, a ferrous sulfate solution is obtained. Add 10% sodium hydroxide to the solution to adjust the pH value to 10, and filter to obtain sludge and high-salt solution. Add ferrous sulfate to the high-salt solution, adjust the pH value to 12, heat at ...
Embodiment 3
[0049] The chromium-containing sludge in a factory area contains 5% chromium, 18% zinc, 4% Cu, 1% Fe, and 1% Ni. Add sulfuric acid to 100g of chromium-containing sludge to dissolve completely, the concentration of acid added is 20%, and the amount of acid added is 200g. After electrolyzing the acid-dissolved solution for 24 hours, the copper in the solution was removed, and the concentration of copper ions in the solution was 16mg / m 3 , 3.8g copper elemental substance was recovered. And use the extraction method to remove the iron in the solution, the iron ion concentration in the solution is 24mg / m 3 . After back-extracting the iron extract, a solution of ferric iron is obtained, and after reduction with excess reduced iron powder, a ferrous sulfate solution is obtained. Add 5% sodium hydroxide to the solution to adjust the pH value to 7, and filter to obtain sludge and high-salt solution. Add ferrous sulfate to the high-salt solution, adjust the pH value to 10, heat at 7...
PUM
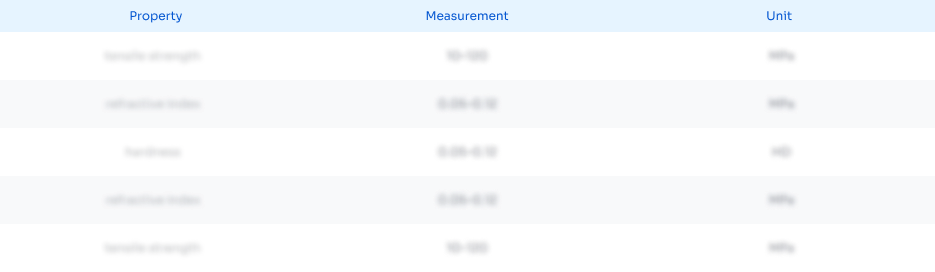
Abstract
Description
Claims
Application Information

- R&D
- Intellectual Property
- Life Sciences
- Materials
- Tech Scout
- Unparalleled Data Quality
- Higher Quality Content
- 60% Fewer Hallucinations
Browse by: Latest US Patents, China's latest patents, Technical Efficacy Thesaurus, Application Domain, Technology Topic, Popular Technical Reports.
© 2025 PatSnap. All rights reserved.Legal|Privacy policy|Modern Slavery Act Transparency Statement|Sitemap|About US| Contact US: help@patsnap.com