Device and method for recovering ammonia and tert-butyl alcohol in cyclohexanone ammoximation production process
A technology for the production process of cyclohexanone amidoxime, which is applied in the recovery device of ammonia and tert-butanol in the production process of cyclohexanone amidoxime, and in the field of cyclohexanone amidoxime production, which can solve the problem of reducing the gas volume and energy entering the vacuum facility Problems such as underutilization and increase of treatment load and energy consumption of cyclohexanone oxime refining system
- Summary
- Abstract
- Description
- Claims
- Application Information
AI Technical Summary
Problems solved by technology
Method used
Image
Examples
Embodiment 1
[0074] According to attached figure 1 In the shown process, in the caprolactam ammoximation reaction device with an annual production capacity of 200,000 tons, the concentration of 35% hydrogen peroxide, ammonia, cyclohexanone, tert-butanol solution and catalyst added in a certain proportion are used in the ammoximation The ammoximation reaction is carried out in the reactor, and the reaction generates an aqueous solution of cyclohexanone oxime. After being filtered by the catalyst, 128.76t / h of the reaction liquid containing tert-butanol, cyclohexanone oxime and water is sent to the reaction liquid pre-separation system, and the reaction tail gas After condensing and cooling, it is sent to the reaction tail gas absorption system, and the reaction tail gas absorption system adopts process water to absorb.
[0075] The reaction liquid is separated from part of ammonia and tert-butanol by the pre-separation system, and then sent to the tert-butanol rectification recovery system....
Embodiment 2
[0078] According to attached figure 1 In the shown process, in the caprolactam ammoximation reaction device with an annual production capacity of 200,000 tons, the concentration of 35% hydrogen peroxide, ammonia, cyclohexanone, tert-butanol solution and catalyst added in a certain proportion are used in the ammoximation The ammoximation reaction is carried out in the reactor, and the cyclohexanone oxime aqueous solution generated by the reaction is filtered by the catalyst, and the reaction liquid containing tert-butanol, cyclohexanone oxime and water is sent to the reaction liquid pre-separation system at 128.76t / h, and the reaction tail gas After condensing and cooling, it is sent to the reaction tail gas absorption system. The reaction tail gas absorption system uses tert-butanol and low-temperature process water for two-stage absorption. The operating pressure of the reaction tail gas alcohol absorption tower is 200kPa.G.
[0079] The reaction solution is sent to the tert-...
Embodiment 3
[0082] According to attached figure 1 In the shown process, in the caprolactam ammoximation reaction device with an annual production capacity of 200,000 tons, the concentration of 60% hydrogen peroxide, ammonia, cyclohexanone, tert-butanol solution and catalyst added in a certain ratio are used in the ammoximation The ammoximation reaction is carried out in the reactor to generate a cyclohexanone oxime aqueous solution. After being filtered by the catalyst, 116.5t / h of the reaction solution containing tert-butanol, cyclohexanone oxime and water is sent to the reaction solution pre-separation system, and the reaction tail gas is passed through After condensing and cooling, it is sent to the reaction tail gas absorption system. The reaction tail gas absorption system uses tert-butanol and low-temperature process water for two-stage absorption. The operating pressure of the reaction tail gas alcohol absorption tower is 200kPa.G.
[0083] The reaction solution is sent to the tert...
PUM
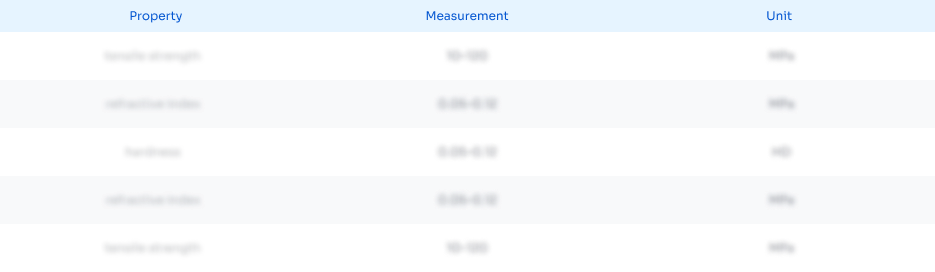
Abstract
Description
Claims
Application Information

- Generate Ideas
- Intellectual Property
- Life Sciences
- Materials
- Tech Scout
- Unparalleled Data Quality
- Higher Quality Content
- 60% Fewer Hallucinations
Browse by: Latest US Patents, China's latest patents, Technical Efficacy Thesaurus, Application Domain, Technology Topic, Popular Technical Reports.
© 2025 PatSnap. All rights reserved.Legal|Privacy policy|Modern Slavery Act Transparency Statement|Sitemap|About US| Contact US: help@patsnap.com