A method to improve the success rate of 3D printing thin-walled metal components
A metal component, 3D printing technology, applied in the direction of improving energy efficiency, process efficiency, additive manufacturing, etc., can solve problems such as labor cost increase, inability to accurately control warpage deformation of thin-walled metal components, repeated failures, etc. The effect of printing success rate and reducing the risk of scraper jamming
- Summary
- Abstract
- Description
- Claims
- Application Information
AI Technical Summary
Problems solved by technology
Method used
Image
Examples
Embodiment 1
[0028] This embodiment provides a method for improving the success rate of 3D printing thin-walled metal components, including the following steps:
[0029] (1) Perform pre-software processing on the digital model of thin-walled metal components, adjust the position of thin-walled metal components in the equipment forming cabin, and ensure that thin-walled metal components can be printed;
[0030] (2) Optimize the digital model of thin-walled metal components that meet the above requirements;
[0031] (3) Adjust the position of the thin-walled metal components to digitally import the parameter data package of the printing material, and then import the 3D printing equipment to prepare for the pre-printing of the equipment. After the preparation is completed, start printing through 3D printing technology;
[0032] (4) After the printing is completed, take out the thin-walled metal components for subsequent processing, and finally complete the delivery of the thin-walled metal co...
Embodiment 2
[0034] On the basis of the above embodiments, this embodiment further defines the material of the thin-walled metal component, the printing material used, and the 3D printing technology used. The thin-walled metal component for 3D printing is a large thin-walled titanium alloy component , the printing material used is titanium alloy TC4 powder, and the 3D printing technology used is laser selective melting forming technology. Other parts of this embodiment are the same as Embodiment 1 and will not be repeated here.
Embodiment 3
[0036] On the basis of the above embodiments, this embodiment further defines the position of the thin-walled metal member in the equipment forming cabin. The structural diagram of the 3D printing equipment forming cabin is as follows figure 1 As shown, in the step (1), the specific process of adjusting the position of the thin-walled metal component in the forming cabin of the equipment is as follows: keep the component as far away from the edge area of the substrate as possible, and reduce the printing height of the component in the cabin as much as possible. The pre-processing digital model adjusts its forming position in the cabin, so that the forming area is as far away from the edge area of the substrate as possible. The heat dissipation in the edge area of the substrate is slow, and the stability of laser energy input is poor. Therefore, staying away from the edge area is beneficial to ensure the quality of components. Reduces the risk of warping.
[0037] As ment...
PUM
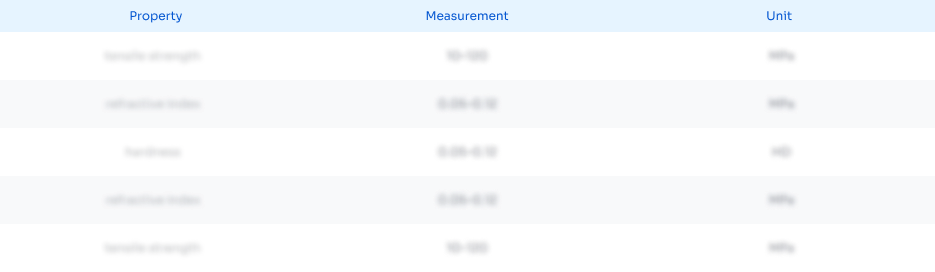
Abstract
Description
Claims
Application Information

- Generate Ideas
- Intellectual Property
- Life Sciences
- Materials
- Tech Scout
- Unparalleled Data Quality
- Higher Quality Content
- 60% Fewer Hallucinations
Browse by: Latest US Patents, China's latest patents, Technical Efficacy Thesaurus, Application Domain, Technology Topic, Popular Technical Reports.
© 2025 PatSnap. All rights reserved.Legal|Privacy policy|Modern Slavery Act Transparency Statement|Sitemap|About US| Contact US: help@patsnap.com