Preparation method of graphene-reinforced silicon nitride-based ceramic
A silicon nitride-based, ceramic preparation technology, applied in the field of structural ceramic materials, can solve the problems of graphene damage, reinforcement and toughness, graphene agglomeration, etc., and achieve the effect of improving fracture toughness and good mechanical properties
- Summary
- Abstract
- Description
- Claims
- Application Information
AI Technical Summary
Problems solved by technology
Method used
Image
Examples
Embodiment 1
[0033] A method for preparing graphene-reinforced silicon nitride-based ceramics includes the following steps:
[0034] Step S1, weighing silicon nitride, graphene, magnesium oxide and yttrium oxide, the mass percentages of which are: graphene: 10wt%, yttrium oxide and alumina 10wt%, silicon nitride: 80wt%, as the main raw materials; Weigh 100% of the graphene mass of PVP (polyvinylpyrrolidone), measure and add graphene, the graphene concentration can reach 1mg / ml NMP (N-methylpyrrolidone), as a dispersant and dispersion medium; yttrium oxide and Alumina is a sintering aid.
[0035] Step S2, pour the graphene and PVP weighed in step S1 into NMP to form a graphene dispersion, which is placed in a 60°C water bath environment for supergenerating dispersion and mechanically stirred for 120 minutes;
[0036] Step S3, pour the aluminum oxide, yttrium oxide and silicon nitride weighed in step S1 into the dispersion in step S2 to obtain a composite raw material dispersion, which is placed i...
Embodiment 2
[0045] A method for preparing graphene-reinforced silicon nitride-based ceramics includes the following steps:
[0046] Step S1, weighing silicon nitride, graphene, magnesium oxide and yttrium oxide, the mass percentages of which are: graphene: 0.5wt%, yttrium oxide and alumina 10wt%, silicon nitride: 89.5wt%, as the main raw materials ; Separately weigh PVP (polyvinylpyrrolidone) with 100% graphene mass, measure and add graphene to NMP (N-methylpyrrolidone) whose graphene concentration can reach 1.5mg / ml, as dispersant and dispersion medium;
[0047] Step S2: Pour the graphene and PVP weighed in step S1 into NMP to form a graphene dispersion, which is placed in a 70°C water bath environment for supergenerating dispersion and mechanically stirred for 120 minutes;
[0048] Step S3, pour the aluminum oxide, yttrium oxide and silicon nitride weighed in step S1 into the dispersion in step S2 to obtain a composite raw material dispersion, which is placed in a 60°C water bath environment f...
Embodiment 3
[0056] A method for preparing graphene-reinforced silicon nitride-based ceramics includes the following steps:
[0057] Step S1, weighing silicon nitride, graphene, magnesium oxide and yttrium oxide, the mass percentages of which are: graphene: 1wt%, yttrium oxide and alumina 10wt%, silicon nitride: 89wt%, as the main raw materials; Weigh 75% of the graphene mass of PVP (polyvinylpyrrolidone), measure and add graphene to NMP (N-methylpyrrolidone) whose graphene concentration can reach 2mg / ml, as a dispersant and dispersion medium;
[0058] Step S2, pour the graphene and PVP weighed in step S1 into NMP to form a graphene dispersion, which is placed in a water bath environment at 80°C for supergenerating dispersion and mechanically stirred for 60 minutes;
[0059] Step S3, pour the aluminum oxide, yttrium oxide and silicon nitride weighed in step S1 into the dispersion in step S2 to obtain a composite raw material dispersion, which is placed in a 60°C water bath environment for superge...
PUM
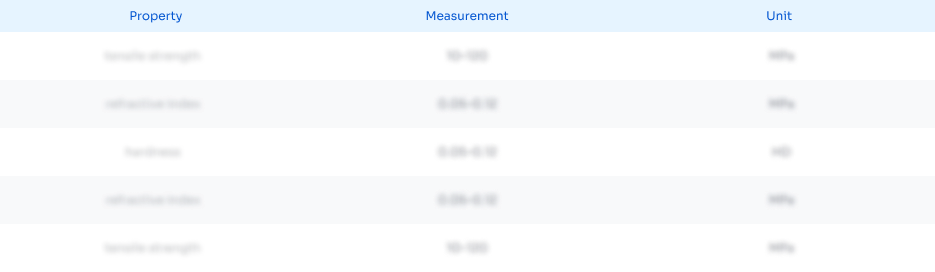
Abstract
Description
Claims
Application Information

- R&D
- Intellectual Property
- Life Sciences
- Materials
- Tech Scout
- Unparalleled Data Quality
- Higher Quality Content
- 60% Fewer Hallucinations
Browse by: Latest US Patents, China's latest patents, Technical Efficacy Thesaurus, Application Domain, Technology Topic, Popular Technical Reports.
© 2025 PatSnap. All rights reserved.Legal|Privacy policy|Modern Slavery Act Transparency Statement|Sitemap|About US| Contact US: help@patsnap.com