Micro-nano mechanical testing experimental platform and method for precision cutting
A technology for testing experiments and precision cutting, which is applied in the direction of measuring/indicating equipment, metal processing machinery parts, metal processing equipment, etc., and can solve problems such as inability to realize in-situ measurement
- Summary
- Abstract
- Description
- Claims
- Application Information
AI Technical Summary
Problems solved by technology
Method used
Image
Examples
Embodiment 1
[0045] A precision cutting micro-nano mechanical testing experimental platform, the main device diagram is as follows figure 1 As shown, it includes a three-axis ultra-precision machine tool 1, a three-way micro-motion table 2, a three-way dynamometer 3, a laser displacement sensor 4, a high-speed camera 5, and a thermal imager 6; the three-way micro-motion table 2 is installed on the three-way On the dynamometer 3, the three-way dynamometer is fixed on the workbench of the three-axis ultra-precision machine tool 1, and the laser displacement sensor 4, the high-speed camera 5, and the thermal imager 6 are focused on the cutting position. The three-axis ultra-precision machine tool 1 includes a machine tool spindle 7 , a machine tool X axis 8 , and a machine tool Z axis 9 . During the cutting process, the three-way dynamometer 3 collects the change process data of the cutting force, the laser displacement sensor 4 collects vibration data, the high-speed camera 5 collects chip f...
Embodiment 2
[0053] The method for implementing the above-mentioned precision cutting micro-nano mechanical testing experimental platform specifically includes the following steps:
[0054] S1. Ensure that the working characteristics of each shaft system of the three-axis ultra-precision machine tool are normal, so that the ultra-precision lathe is warmed up until the lathe reaches thermal stability; install the tool of the ultra-precision lathe, and complete the dynamic balance adjustment of the tool;
[0055] S2 Install the sample on the three-way micro-motion table, and the three-way micro-motion table is installed on the three-way dynamometer; the tool setting process is realized by adjusting the three-way micro-motion table;
[0056] S3. Turn on the three-way dynamometer, laser displacement sensor, high-speed camera, and thermal imager; focus the laser displacement sensor, high-speed camera, and thermal imager on the cutting position of the three-axis ultra-precision machine tool to mo...
PUM
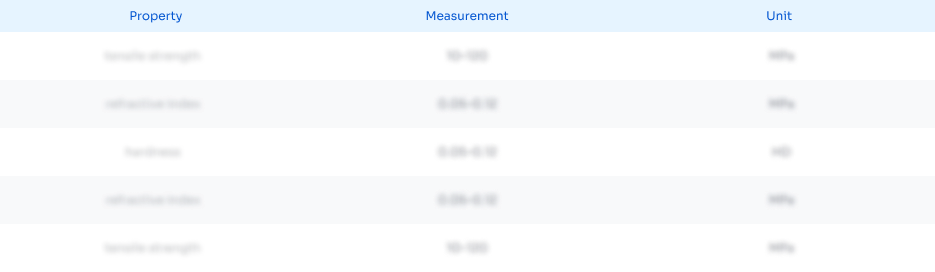
Abstract
Description
Claims
Application Information

- R&D
- Intellectual Property
- Life Sciences
- Materials
- Tech Scout
- Unparalleled Data Quality
- Higher Quality Content
- 60% Fewer Hallucinations
Browse by: Latest US Patents, China's latest patents, Technical Efficacy Thesaurus, Application Domain, Technology Topic, Popular Technical Reports.
© 2025 PatSnap. All rights reserved.Legal|Privacy policy|Modern Slavery Act Transparency Statement|Sitemap|About US| Contact US: help@patsnap.com