Five-axis grinding robot
A robot and grinding technology, applied in the field of robotics, can solve the problems of increased cumulative error, limited load capacity of the sixth axis, limited installation space, etc., and achieve the goal of reducing cumulative error, improving internal space utilization, and high rigidity and flexibility Effect
- Summary
- Abstract
- Description
- Claims
- Application Information
AI Technical Summary
Problems solved by technology
Method used
Image
Examples
Embodiment 1
[0070] see figure 1, in one embodiment, a five-axis grinding robot, comprising: a mechanical arm, a U-shaped structure 11, a power spindle 12, a tool magazine; the first end of the mechanical arm is located on an external platform, and the second end of the mechanical arm The end is connected with the U-shaped structural member 11, and the power spindle 12 is arranged on the U-shaped structural member 11; the mechanical arm includes a base 1, a first connecting rod 2, a second connecting rod 3, a third connecting rod 4, and a fourth connecting rod 5. The first joint 6, the second joint 7, the third joint 8, the fourth joint 9 and the fifth joint 13; the first end of the base 1 is connected to the external platform; the first end of the first connecting rod 2 is connected to the base The second end of seat 1 is rotationally connected through first joint 6; the first end of second connecting rod 3 is rotationally connected with the second end of first connecting rod 2 through se...
Embodiment 2
[0104] Different from Embodiment 1, this example also can not use the U-shaped structural member 11, directly do modification on the power main shaft 12, directly set the convex piece, and the branch structure can also be connected by the convex piece. Or, in this example, other intermediate connectors can also be set to realize the connection, as long as the power main shaft 12 can be connected to the branch structure, and the rotation control of the power main shaft 12 can be realized under the action of the fifth joint 13. Can.
[0105] That is, a five-axis grinding robot includes: a mechanical arm, a power spindle 12, and a tool magazine. The first end of the mechanical arm is arranged on an external platform, and the second end of the mechanical arm is connected to the power spindle 12 or an intermediate connector. The mechanical arm includes a base 1, a first link 2, a second link 3, a third link 4, a fourth link 5, a first joint 6, a second joint 7, a third joint 8, and...
PUM
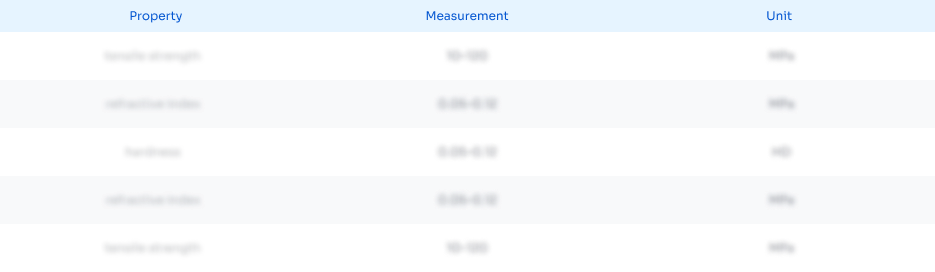
Abstract
Description
Claims
Application Information

- R&D Engineer
- R&D Manager
- IP Professional
- Industry Leading Data Capabilities
- Powerful AI technology
- Patent DNA Extraction
Browse by: Latest US Patents, China's latest patents, Technical Efficacy Thesaurus, Application Domain, Technology Topic, Popular Technical Reports.
© 2024 PatSnap. All rights reserved.Legal|Privacy policy|Modern Slavery Act Transparency Statement|Sitemap|About US| Contact US: help@patsnap.com