Catalyst for preparing H2 by direct cracking of methanol, and preparation method and application of catalyst
A catalyst and methanol technology, which is applied in the field of hydrogen production from methanol, can solve the problems affecting the economic cost and competitiveness of hydrogen production, side reactions, etc., and achieve the effects of high stability, high selectivity and high activity
- Summary
- Abstract
- Description
- Claims
- Application Information
AI Technical Summary
Problems solved by technology
Method used
Image
Examples
Embodiment 1
[0032] Such as figure 1 As shown, a direct cleavage of methanol to produce H 2 Catalyst and its application, copper cobalt bimetallic catalyst preparation precursor is copper nitrate (Cu(NO 3 ) 2 ) and cobalt nitrate (Co(NO 3 ) 2 ) mixed solution, the co-catalyst precursor is lanthanum nitrate series (La(NO 3 ) 3 ) and modified enhancer as potassium nitrate (KNO 3 ) mixed solution, the carrier is pretreated multi-layered carbon nanotubes (CNTs), the matrix is magnesium oxide (MgO), and the active component copper containing 20-25% (w / w, below similar), 10% to 15% cobalt, 3% to 5% lanthanum containing catalyst promoter, 3% to 5% potassium promoter, and the rest is a solid catalyst containing CNTs and MgO mixed carrier, and methanol anaerobic Catalytic direct cracking to produce hydrogen (H 2 ) and methanol anaerobic catalytic thermal cracking reaction of by-product carbon monoxide (CO):
[0033] (1) The raw material is industrial methanol (liquid), after gasification...
Embodiment 2
[0038] The pretreatment of the multilayer carbon nanotube CNTs described in Example 1 is to add about 1 to 2 g of commercially available CNTs carriers with a specification of 10 nm into a total volume of about 230 to 260 mL of nitric acid with a mass concentration of 30% and about 70% In the mixed solution of nitric acid with mass concentration, heat to 110-120°C, stir evenly, and azeotropically reflux at 110-120°C for 6-8 hours, cool to ambient temperature, vacuum filter, and wash with deionized water for two After three times to neutrality, the resulting filter cake is dried at 120°C for 1-2 hours, ground into 10-20nm powder, mixed with 1-1.5g of MgO powder, roasted and cooled under nitrogen flow at 630-660°C A mixed carrier of CNTs and MgO is formed to support active components Cu, Co, cocatalyst La, and promoter K.
Embodiment 3
[0040] On the basis of Embodiment 1 and 2, the preparation of MgO in the mixed carrier is that about 5~7g oxalic acid (H 2 C 2 o 4 ) and 7~9g magnesium acetate (Mg(CH 3 COO) 3 ) were dissolved in 200-240mL and 50-70mL deionized water respectively, and the magnesium acetate solution was poured into the oxalic acid solution and stirred for about 3-5 hours to produce a precipitate, which was taken out and washed continuously with deionized water for 2-3 hours. Once again, dry at 70-80°C for 1-2 hours, then grind it into powder, and bake it at 650-700°C and nitrogen flow for 3-4 hours. / h, at 120-140°C / 2h in the late stage of heating up, take it out after being purged with nitrogen and cooled to ambient temperature, and mix with the treated CNTs to form a catalyst carrier.
PUM
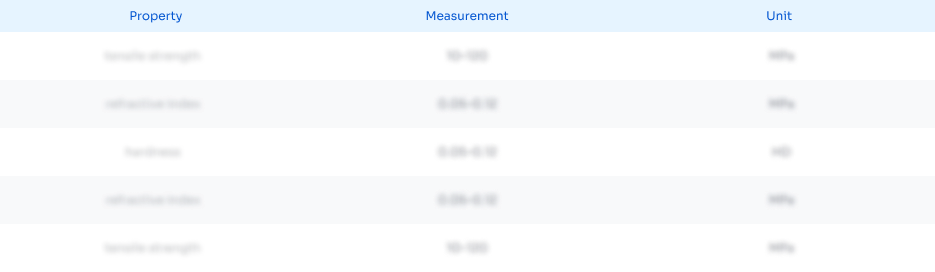
Abstract
Description
Claims
Application Information

- Generate Ideas
- Intellectual Property
- Life Sciences
- Materials
- Tech Scout
- Unparalleled Data Quality
- Higher Quality Content
- 60% Fewer Hallucinations
Browse by: Latest US Patents, China's latest patents, Technical Efficacy Thesaurus, Application Domain, Technology Topic, Popular Technical Reports.
© 2025 PatSnap. All rights reserved.Legal|Privacy policy|Modern Slavery Act Transparency Statement|Sitemap|About US| Contact US: help@patsnap.com