Sound insulation composite material and preparation method thereof
A composite material and raw material technology, which is applied in the field of material processing, can solve the problems of high material density and mechanical properties, and deviation from the trend of lightweight automobiles, and achieve the effects of long service life, low product cost, and improved mechanical properties.
- Summary
- Abstract
- Description
- Claims
- Application Information
AI Technical Summary
Problems solved by technology
Method used
Examples
Embodiment 1
[0023] A sound-insulating composite material, comprising the following raw materials in parts by weight: 120 kg of epoxy resin, 10 kg of modified hollow glass microspheres, 80 kg of methylhexahydrophthalic anhydride, 1 kg of 2-ethyl-4-methylimidazole, and liquid carboxy-terminated butyl The blend of nitrile rubber and EP-51 type epoxy resin 10kg.
[0024] A method for preparing a sound-insulating composite material, comprising the steps of:
[0025] (1) Preparation of modified hollow glass microspheres: soak the hollow glass microspheres in an alkaline solution, stir for 6 hours, stop stirring and leave to soak for 24 hours, then repeatedly wash with distilled water and suction filter until the pH of the filtrate is neutral. Vacuum drying at constant temperature at 60°C, adding a mixture of ethanol and distilled water and ammonia water to the dried hollow glass microspheres, the volume ratio of ethanol and distilled water in the mixture of ethanol and distilled water is 1:1, u...
Embodiment 2
[0029] A sound-insulating composite material, prepared from the following raw materials in parts by weight: 150 kg of epoxy resin, 30 kg of modified hollow glass microspheres, 90 kg of methyl hexahydrophthalic anhydride, 1.5 kg of 2-ethyl-4-methylimidazole, and liquid carboxyl-terminated The blend of nitrile rubber and EP-51 type epoxy resin 12kg.
[0030] A method for preparing a sound-insulating composite material, comprising the steps of:
[0031] (1) Preparation of modified hollow glass microspheres: soak the hollow glass microspheres in an alkaline solution, stir for 8 hours, stop stirring and let stand for soaking for 30 hours, then repeatedly wash with distilled water and suction filter until the pH of the filtrate is neutral. Vacuum drying at a constant temperature of 65°C, adding a mixture of ethanol and distilled water and ammonia water to the dried hollow glass microspheres, the volume ratio of ethanol and distilled water in the mixture of ethanol and distilled wate...
Embodiment 3
[0035] A sound-insulating composite material, which is prepared from the following raw materials in parts by weight: 155kg of epoxy resin, 35kg of modified hollow glass microspheres, 100kg of methyl hexahydrophthalic anhydride, 2 parts of accelerator, liquid carboxy-terminated nitrile rubber and EP-51 type Epoxy blend 15 parts.
[0036] A method for preparing a sound-insulating composite material, comprising the steps of:
[0037](1) Preparation of modified hollow glass microspheres: soak the hollow glass microspheres in an alkaline solution, stir for 6 hours, stop stirring and leave to soak for 36 hours, then repeatedly wash with distilled water and suction filter until the pH of the filtrate is neutral. Vacuum drying at a constant temperature of 65°C, adding a mixture of ethanol and distilled water and ammonia water to the dried hollow glass microspheres, the volume ratio of ethanol and distilled water in the mixture of ethanol and distilled water is 1:1, ultrasonic dispersi...
PUM
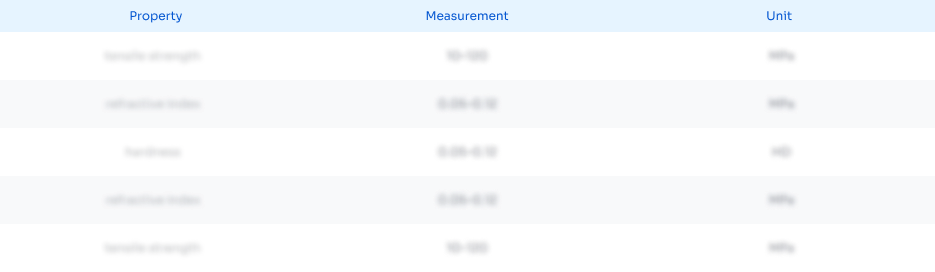
Abstract
Description
Claims
Application Information

- Generate Ideas
- Intellectual Property
- Life Sciences
- Materials
- Tech Scout
- Unparalleled Data Quality
- Higher Quality Content
- 60% Fewer Hallucinations
Browse by: Latest US Patents, China's latest patents, Technical Efficacy Thesaurus, Application Domain, Technology Topic, Popular Technical Reports.
© 2025 PatSnap. All rights reserved.Legal|Privacy policy|Modern Slavery Act Transparency Statement|Sitemap|About US| Contact US: help@patsnap.com