Preparation method of olefin-olefin alcohol copolymer
A technology for olefin alcohols and copolymers, which is applied in the field of preparation of olefin-olefin alcohol copolymers, can solve the problems of polymer transport solvent removal, difficult granulation, fouling, etc., and achieve good industrial application prospects and good morphology Effect
- Summary
- Abstract
- Description
- Claims
- Application Information
AI Technical Summary
Problems solved by technology
Method used
Image
Examples
Embodiment 1
[0104] 1) Preparation of ligand:
[0105] 1.5ml 2,6-dimethylaniline (12mmol) was reacted with 57ml 1M trimethylaluminum in toluene, after reflux for 3h, camphorquinone (1.05g, 5mmol) was added, and the reaction was reflux for 8 hours. The reaction was terminated with sodium / ice water, extracted with ethyl acetate, the organic phases were combined, and dried over anhydrous magnesium sulfate. The product was separated by petroleum ether / ethyl acetate column chromatography to obtain a colorless crystal ligand L1 with a yield of 70.2%. 1 HNMRδ(ppm)7.00-6.89(m,6H,Ar-H),3.57(s,1H,NH),2.18(s,6H,CAr-CH 3 ),2.05(s,6H,CH 3 ),1.74(m,4H,CH 2 ),1.44(s,3H,CH 3 ),1.35(m,1H),1.21(s,3H,CH 3 ),1.01(s,3H,CH 3 ),0.87(s,3H,CH 3 ).
[0106] 2) Preparation of complex 1: 10ml (DME) NiBr 2 (277mg, 0.9mmol) in dichloromethane solution was added dropwise to 10ml of ligand L1 (350mg, 0.9mmol) in dichloromethane solution, stirred at room temperature for 6 hours, a precipitate precipitated, filtere...
Embodiment 2
[0109] Dry the 1L stainless steel polymerization kettle equipped with mechanical stirring at 130 ° C for 6 hours, vacuumize while it is hot and use N 2 Gas replacement 3 times. Inject 500 mL of hexane into the polymerization system, and simultaneously add 6.1 mg (10 μmol) of complex 1, 30 mmol (5.1 mL) of 2-methyl-2-hydroxy-7-octene, 30 mL of AlEt 3 (1.0mol / L hexane solution), 6.5mL MAO (1.53mol / L toluene solution), at 20°C, keep ethylene pressure of 10atm, and stir for 30min. Finally, it was neutralized with an ethanol solution acidified with 5 volume % hydrochloric acid to obtain a polymer. The polymerization activity and the performance parameters of the polymer are shown in Table 1.
[0110] figure 1 and figure 2 The electron micrographs of the spherical and / or quasi-spherical polymer prepared in this embodiment and after cutting are shown, and it can be seen that the spherical polymer has a cavity inside.
Embodiment 3
[0112] Dry the 1L stainless steel polymerization kettle equipped with mechanical stirring at 130 ° C for 6 hours, vacuumize while it is hot and use N 2 Gas replacement 3 times. Inject 500 mL of hexane into the polymerization system, and simultaneously add 6.1 mg (10 μmol) of complex 1, 30 mmol (5.1 mL) of 2-methyl-2-hydroxy-7-octene, 30 mL of AlEt 3 (1.0mol / L hexane solution), 6.5mL MAO (1.53mol / L toluene solution), at 60°C, keep 10atm ethylene pressure, and stir for 30min. Finally, it was neutralized with an ethanol solution acidified with 5 volume % hydrochloric acid to obtain a polymer. The polymerization activity and the performance parameters of the polymer are shown in Table 1.
PUM
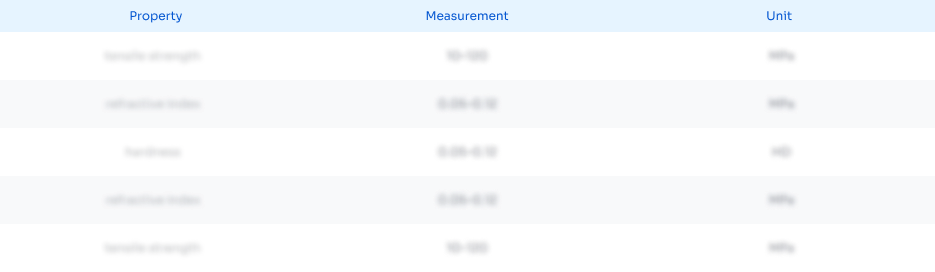
Abstract
Description
Claims
Application Information

- R&D
- Intellectual Property
- Life Sciences
- Materials
- Tech Scout
- Unparalleled Data Quality
- Higher Quality Content
- 60% Fewer Hallucinations
Browse by: Latest US Patents, China's latest patents, Technical Efficacy Thesaurus, Application Domain, Technology Topic, Popular Technical Reports.
© 2025 PatSnap. All rights reserved.Legal|Privacy policy|Modern Slavery Act Transparency Statement|Sitemap|About US| Contact US: help@patsnap.com