A kind of non-slip TPR outsole and preparation method thereof
A technology of anti-slip sheet and internal mixer, applied in the direction of shoe soles, clothing, footwear, etc., can solve the problem of snow layer, thin ice, frozen soil layer, failure to reach the target anti-slip coefficient, failure to decompose, recycle and reuse, etc. Problems, to achieve good social benefits, anti-aging performance improvement, the effect of low density
- Summary
- Abstract
- Description
- Claims
- Application Information
AI Technical Summary
Problems solved by technology
Method used
Image
Examples
Embodiment 1
[0040] A preparation method for an anti-slip TPR outsole, comprising the following steps:
[0041] Step 1, preparation of anti-slip sheet: 5 parts by weight of butadiene rubber, 8 parts of styrene-butadiene rubber, 8 parts of isoprene rubber, 8 parts of solution polystyrene-butadiene rubber, 10 parts of nitrile rubber, white carbon black Put 10 parts, 2 parts of cold-resistant plasticizer, 0.5 parts of anti-aging agent, 2.5 parts of white smoke active agent, 0.5 parts of polyethylene wax, and 1 part of anti-vomiting cream into the internal mixer, and mix them evenly at a temperature of 105 degrees 15min;
[0042] Step 2. Preparation of anti-slip sheet: Add 3 parts of carbon fiber, 3 parts of nylon fiber, 10 parts of glass fiber, 2 parts of silane coupling agent, and 2 parts of phenolic resin into step 1, keep the temperature constant, and continue to mix for 15 minutes;
[0043] Step 3. Preparation of anti-slip sheet: Add 0.5 parts of sulfur and 2.2 parts of vulcanization acc...
Embodiment 2
[0049]A preparation method for an anti-slip TPR outsole, comprising the following steps:
[0050] Step 1, preparation of anti-slip sheet: 10 parts of butadiene rubber, 12 parts of styrene-butadiene rubber, 12 parts of isoprene rubber, 12 parts of solution-polymerized styrene-butadiene rubber, 15 parts of nitrile rubber, white carbon black in parts by weight Put 15 parts, 4 parts of cold-resistant plasticizer, 1 part of anti-aging agent, 2.6 parts of white smoke active agent, 1 part of polyethylene wax, and 1.5 parts of anti-vomiting cream into the internal mixer, and mix them evenly at a temperature of 105 degrees 15min;
[0051] Step 2. Preparation of anti-slip sheet: add 4 parts of carbon fiber, 4 parts of nylon fiber, 12 parts of glass fiber, 3.5 parts of silane coupling agent, and 2.5 parts of phenolic resin into step 1, keep the temperature unchanged, and continue to mix for 15 minutes;
[0052] Step 3. Preparation of anti-slip sheet: Add 2.5 parts of sulfur and 2.3 part...
Embodiment 3
[0058] A preparation method for an anti-slip TPR outsole, comprising the following steps:
[0059] Step 1, the preparation of anti-slip sheet: 15 parts by weight of butadiene rubber, 15 parts of styrene-butadiene rubber, 15 parts of isoprene rubber, 15 parts of solution-polymerized styrene-butadiene rubber, 20 parts of nitrile rubber, white carbon black Put 20 parts, 6 parts of cold-resistant plasticizer, 1.5 parts of anti-aging agent, 2.6 parts of white smoke active agent, 1.5 parts of polyethylene wax, and 2 parts of anti-vomiting cream into the internal mixer, and mix them evenly at a temperature of 105 degrees 15min;
[0060] Step 2. Preparation of anti-slip sheet: add 5 parts of carbon fiber, 5 parts of nylon fiber, 15 parts of glass fiber, 5 parts of silane coupling agent, and 3 parts of phenolic resin into step 1, keep the temperature constant, and continue to mix for 15 minutes;
[0061] Step 3. Preparation of anti-slip sheet: Add 4 parts of sulfur and 2.3 parts of vu...
PUM
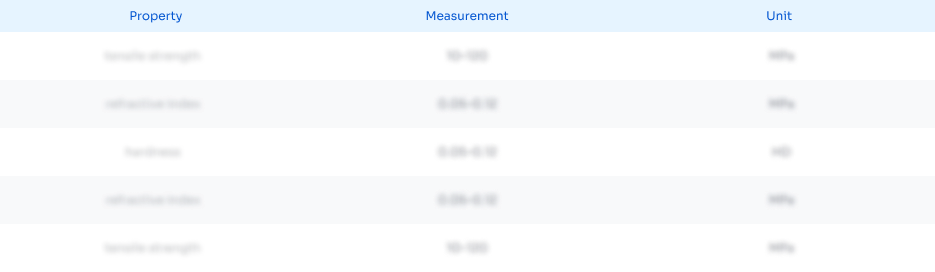
Abstract
Description
Claims
Application Information

- Generate Ideas
- Intellectual Property
- Life Sciences
- Materials
- Tech Scout
- Unparalleled Data Quality
- Higher Quality Content
- 60% Fewer Hallucinations
Browse by: Latest US Patents, China's latest patents, Technical Efficacy Thesaurus, Application Domain, Technology Topic, Popular Technical Reports.
© 2025 PatSnap. All rights reserved.Legal|Privacy policy|Modern Slavery Act Transparency Statement|Sitemap|About US| Contact US: help@patsnap.com