Method for preparing resin from phenyl alkoxy silane high-boiling residue
A technology of phenylalkoxysilane and high boiler, which is applied in the field of preparing resin from phenylalkoxysilane high boiler, can solve the problems of poor mechanical properties of vulcanizate, difficult to control, complicated and tedious preparation process, etc. Inexpensive, inexpensive and flexible
- Summary
- Abstract
- Description
- Claims
- Application Information
AI Technical Summary
Problems solved by technology
Method used
Examples
Embodiment 1
[0016] Embodiment 1, a kind of method for preparing resin from phenylalkoxysilane high boiler comprises the following steps:
[0017] Press the phenylalkoxysilane high boiler, chlorosilane monomer, and part of the solvent into the dripping kettle by the feed pump for standby; part of the solvent, water, and alcohol are mixed into the reaction kettle, and the materials in the dropping kettle are added dropwise In the reaction kettle, control the reaction temperature at 15-55°C, and the dropwise addition time is 3-8h; after the dropwise addition, stir for 1-3h to separate the acidic water layer, and wash the silicone resin prepolymer 3-6 times to medium After deactivation, filter, evaporate the solvent, add a catalyst to polymerize, and add a solvent to cool down to obtain the finished phenyl silicone resin.
[0018] Among them, phenylalkoxysilane high boilers include high boilers produced by the production of phenyltrimethoxysilane and phenyltriethoxysilane;
[0019] Wherein, ...
Embodiment 2
[0023] Embodiment 2, a method for preparing resin from phenylalkoxysilane high boilers, comprising the following steps: 212 parts of phenylalkoxysilane high boilers, 45 parts of methyltrichlorosilane, 67 parts of dimethyl Dichlorosilane and 430 parts of xylene are pressed into the dripping kettle by the feed pump for subsequent use; 210 parts of toluene, 561 parts of water, and 242 parts of ethanol are allocated in the reactor, and the material in the dripping kettle is added dropwise in the reactor. Control the reaction temperature at 25-35°C, and the dropwise addition time is about 4 hours; after the dropwise addition, stir for 2 hours to separate the lower layer of acidic water, wash the upper layer of silicone resin prepolymer with water for 6 times until neutral, filter, and evaporate the solvent at low temperature Add 0.006 parts of manganese naphthenate, polymerize under reduced pressure at 140°C, add a solvent and cool down to get the finished phenyl silicone resin, the...
Embodiment 3
[0024] Embodiment 3, a method for preparing resin from phenylalkoxysilane high boilers, comprising the following steps: 183 parts of phenylalkoxysilane high boilers, 29 parts of methyltrichlorosilane, 76 parts of dimethyl Dichlorosilane, 51 parts of diphenyldichlorosilane, and 418 parts of xylene are pressed into the dripping kettle by the feed pump for standby; 324 parts of toluene, 411 parts of water, and 256 parts of methanol are allocated in the reaction kettle, and the dripping kettle Add the material in the reaction kettle dropwise, control the reaction temperature at 20-30°C, and drop the time for about 5 hours; after the drop is completed, stir for 2 hours to separate the lower layer of acid water, and wash the upper layer of silicone resin prepolymer with water for 5 times to After neutralization, filter, evaporate the solvent at low temperature, add 0.01 part of butyl titanate and polymerize under reduced pressure at 150°C, add solvent and cool down to get the finishe...
PUM
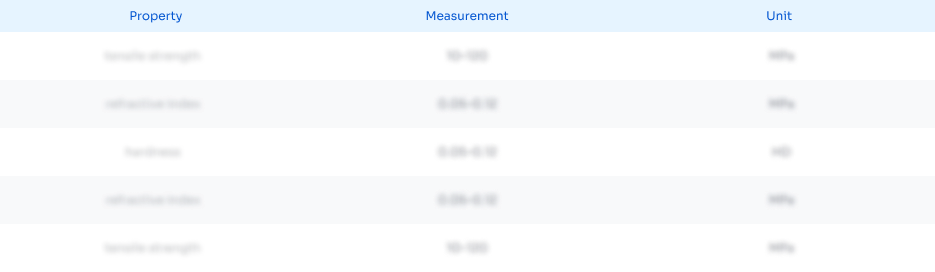
Abstract
Description
Claims
Application Information

- R&D Engineer
- R&D Manager
- IP Professional
- Industry Leading Data Capabilities
- Powerful AI technology
- Patent DNA Extraction
Browse by: Latest US Patents, China's latest patents, Technical Efficacy Thesaurus, Application Domain, Technology Topic, Popular Technical Reports.
© 2024 PatSnap. All rights reserved.Legal|Privacy policy|Modern Slavery Act Transparency Statement|Sitemap|About US| Contact US: help@patsnap.com