Fire-resistant cable manufacturing method
A production method and technology of fire-resistant cables, which are applied in the manufacture of cables/conductors, insulation of conductors/cables, circuits, etc., can solve the problems of reduced fire resistance, good data transmission, and low market promotion rate, and achieve excellent fire resistance. The production process is simple and the effect of normal transmission is guaranteed
- Summary
- Abstract
- Description
- Claims
- Application Information
AI Technical Summary
Problems solved by technology
Method used
Examples
Embodiment Construction
[0028] The following are specific examples of the present invention to further describe the technical solutions of the present invention, but the present invention is not limited to these examples.
[0029] This embodiment provides a method for making a fire-resistant cable, comprising the following steps:
[0030] (1) Conductor production: stranded conductor;
[0031] (2) Insulation production: Extrude the outer layer of insulation on the conductor to form an insulated core;
[0032] (3) Refractory production: wrap a mica layer with hot-melt adhesive on the inner surface of the insulated wire core, fix it with cable ties, and then send it into an oven for heating to make the mica layer and the insulating outer layer, the The above-mentioned mica layers are closely bonded to form a refractory wire core; the mica layer can be selected from conventionally used mica tape, and its width is set according to the diameter of the conductor it covers, generally set to a width slightly...
PUM
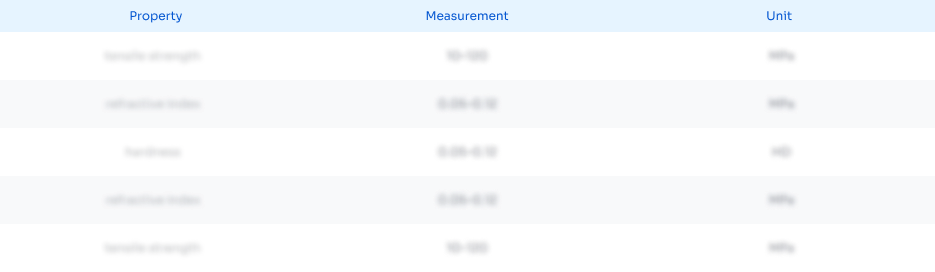
Abstract
Description
Claims
Application Information

- Generate Ideas
- Intellectual Property
- Life Sciences
- Materials
- Tech Scout
- Unparalleled Data Quality
- Higher Quality Content
- 60% Fewer Hallucinations
Browse by: Latest US Patents, China's latest patents, Technical Efficacy Thesaurus, Application Domain, Technology Topic, Popular Technical Reports.
© 2025 PatSnap. All rights reserved.Legal|Privacy policy|Modern Slavery Act Transparency Statement|Sitemap|About US| Contact US: help@patsnap.com