Buoyancy ultrahigh molecular weight polyethylene fibers and preparation method thereof
An ultra-high molecular weight, polyethylene fiber technology, applied in the direction of single-component polyolefin artificial filament, fiber chemical characteristics, rayon manufacturing, etc., can solve the problems of bulletproof, anti-stab and anti-cut products, and achieve good floating performance , light weight, and improved floating performance
- Summary
- Abstract
- Description
- Claims
- Application Information
AI Technical Summary
Problems solved by technology
Method used
Examples
Embodiment 1
[0024] A preparation method for buoyant ultra-high molecular weight polyethylene fibers, comprising the steps of:
[0025] (1) Preheat 71.68g of epoxy resin, heat to 60°C for 30min, degas at 50°C for 1h, add 4.72g of low molecular weight polyamide resin and stir quickly, put it into the drying oven again for degassing for 60min; continue stirring Epoxy resin, add 7.13g hollow glass microspheres while stirring, mix well and let stand for 40min;
[0026] (2) Prepare the coupling agent KH-560 and ethanol solution to form a silane solution with a mass fraction of 15%-, stir the silane solution for 40 minutes, add it to step (1), stir rapidly for 65 minutes, and dry at 80°C for 3.2 hours , to obtain activated hollow glass microspheres;
[0027] (3) Mix the hollow glass microspheres obtained in step (2) with the ultra-high molecular weight polyethylene solution in a swelling kettle at a mass ratio of 1:50, stir and heat up to 30°C, and keep warm for 1.2h to form a spinning fluid ;...
Embodiment 2
[0030] A preparation method for buoyant ultra-high molecular weight polyethylene fibers, comprising the steps of:
[0031] (1) Preheat 71.68g of epoxy resin, heat it to 70°C for 25min, degas at 60°C for 1h, add 4.72g of low molecular weight polyamide resin and stir quickly, put it into the drying oven again for degassing for 55min; continue stirring Epoxy resin, add 7.13g hollow glass microspheres while stirring, mix well and let stand for 45min;
[0032] (2) Prepare the coupling agent KH-560 and ethanol solution to form a silane solution with a mass fraction of 18%, stir the silane solution for 48 minutes, add it to step (1), stir rapidly for 56 minutes, and dry at 90°C for 2.8 hours. Obtain the activated hollow glass microspheres;
[0033] (3) Mix the hollow glass microspheres obtained in step (2) with the ultra-high molecular weight polyethylene solution in a swelling kettle at a mass ratio of 1:60, stir and heat up to 40°C, and keep warm for 1.0h to form a spinning fluid ...
Embodiment 3
[0036] A preparation method for buoyant ultra-high molecular weight polyethylene fibers, comprising the steps of:
[0037] (1) Preheat 71.68g of epoxy resin, heat it to 85°C for 20min, degas at 75°C for 1h, add 4.72g of low molecular weight polyamide resin and stir quickly, put it into the drying oven again for degassing for 50min; continue stirring Epoxy resin, add 7.13g hollow glass microspheres while stirring, mix well and let stand for 50min;
[0038] (2) Prepare the coupling agent KH-560 and ethanol solution to form a silane solution with a mass fraction of 20%, stir the silane solution for 55 minutes, add it to step (1), stir it rapidly for 50 minutes, and dry it at 100°C for 2.5 hours. Obtain the activated hollow glass microspheres;
[0039] (3) Mix the hollow glass microspheres obtained in step (2) with the ultra-high molecular weight polyethylene solution in a swelling kettle at a mass ratio of 1:70, stir and heat up to 30°C, and keep warm for 1.2h to form a spinning...
PUM
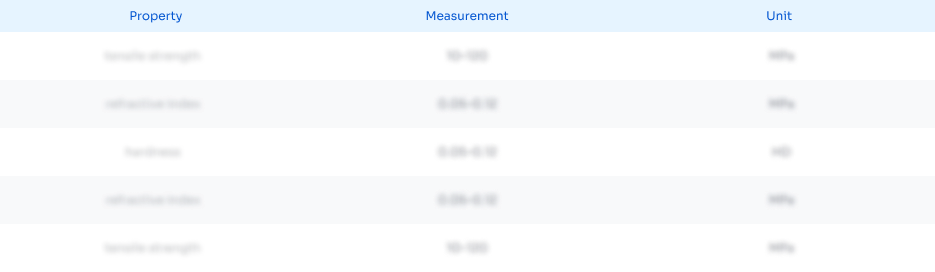
Abstract
Description
Claims
Application Information

- Generate Ideas
- Intellectual Property
- Life Sciences
- Materials
- Tech Scout
- Unparalleled Data Quality
- Higher Quality Content
- 60% Fewer Hallucinations
Browse by: Latest US Patents, China's latest patents, Technical Efficacy Thesaurus, Application Domain, Technology Topic, Popular Technical Reports.
© 2025 PatSnap. All rights reserved.Legal|Privacy policy|Modern Slavery Act Transparency Statement|Sitemap|About US| Contact US: help@patsnap.com