Preparation method and application of cardanol-based waterborne epoxy resin curing agent
A water-based epoxy resin, cardanol-based technology, applied in the direction of epoxy resin coatings, coatings, etc., can solve the problems of increasing energy consumption and environmental protection pressure, and achieve the reduction of environmental protection pressure, good compatibility and good stability Effect
- Summary
- Abstract
- Description
- Claims
- Application Information
AI Technical Summary
Problems solved by technology
Method used
Image
Examples
Embodiment 1
[0030] This embodiment includes the following steps:
[0031] (1) Put 160g of PPG4000 (polypropylene glycol 4000) and 15.2g of epoxy resin E51 (epoxy equivalent 190) into a 500mL glass reactor with reflux condenser and automatic temperature control, heat and melt, start stirring, and mix well , heated up to 100°C, and kept at a constant temperature, 1mL of boron trifluoride ether solution (46.5% by mass) was added within 3 hours, and then reacted at constant temperature for 1 hour, and then cooled to 65°C to obtain an emulsified epoxy functional group agent;
[0032] (2) Put 60g of ethylenediamine and 300g of cardanol into a 1000mL glass reactor with a reflux condenser and automatic temperature control, stir and mix evenly, heat up to 80°C, and add 31g of solid formaldehyde in batches to control The reaction temperature does not exceed 90°C, and then reacts at a constant temperature for 2 hours, vacuumizes and dehydrates for 1 hour (by mass, the water content is less than 2.5...
Embodiment 2
[0038] This embodiment includes the following steps:
[0039] (1) Put 128g PEG4000 and 12.2g E51 epoxy resin (epoxy equivalent 190) into a 500mL glass reactor with reflux condenser and automatic temperature control, heat and melt, start stirring, mix well, and heat up to 100 ℃, and keep the constant temperature, add 0.85mL boron trifluoride ether solution (46.5% by mass) within 3 hours, and then react at constant temperature for 1 hour. Cool to 65 DEG C then, obtain epoxy functional group emulsifier;
[0040] (2) In a 1000mL glass reactor with a reflux condenser and automatic temperature control, put 100g of diethylenetriamine and 240g of cardanol respectively, stir and mix evenly, heat up to 80°C, and put in 30g of solid formaldehyde in batches , control the reaction temperature not to exceed 90°C, then react at a constant temperature for 2 hours, vacuumize and dehydrate for 1 hour (by mass, the water content is lower than 2.5%), and cool to 60°C to obtain the cardanol modif...
Embodiment 3
[0043] This embodiment includes the following steps:
[0044] (1) Put 128g PEG2000 and 28.2g E44 epoxy resin (epoxy equivalent weight 220) into a 500mL glass reactor with reflux condenser and automatic temperature control, heat and melt, start stirring, mix well, and heat up to 100°C , and keep a constant temperature, drop into 0.8mL boron trifluoride ether solution (mass percentage is 46.5%) within 3 hours, then react at a constant temperature for 1 hour, then cool to 65°C to obtain an epoxy functional group emulsifier;
[0045](2) Put 24g of ethylenediamine, 40g of diethylenetriamine, and 240g of cardanol into a 1000ml glass reactor with reflux condenser and automatic temperature control, stir and mix evenly, heat up to 80°C, and divide into batches Put in 25g of solid formaldehyde once, control the reaction temperature not to exceed 90°C, then react at constant temperature for 2 hours, vacuumize and dehydrate for 1 hour (by mass, the water content is less than 2.5%), cool t...
PUM
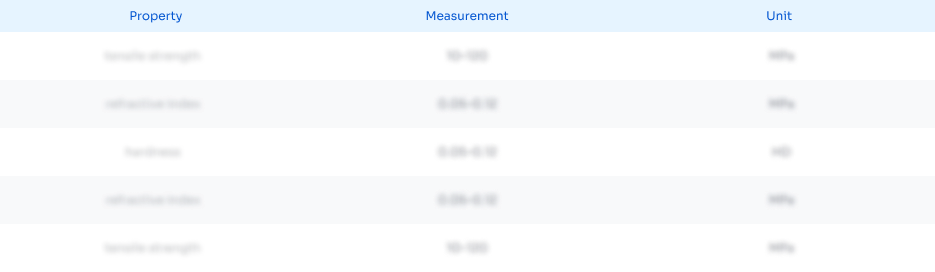
Abstract
Description
Claims
Application Information

- Generate Ideas
- Intellectual Property
- Life Sciences
- Materials
- Tech Scout
- Unparalleled Data Quality
- Higher Quality Content
- 60% Fewer Hallucinations
Browse by: Latest US Patents, China's latest patents, Technical Efficacy Thesaurus, Application Domain, Technology Topic, Popular Technical Reports.
© 2025 PatSnap. All rights reserved.Legal|Privacy policy|Modern Slavery Act Transparency Statement|Sitemap|About US| Contact US: help@patsnap.com