Digital full-automatic production line design method for gas compressor blades
A design method, production line technology, applied to other manufacturing equipment/tools, manufacturing tools, etc.
- Summary
- Abstract
- Description
- Claims
- Application Information
AI Technical Summary
Problems solved by technology
Method used
Image
Examples
Embodiment 1
[0073] A digital full-automatic production line design method for compressor blades, comprising the following steps:
[0074] ①According to the structural requirements of the blade design, based on the structural characteristics of the double journal, citrus plate, blade body and small-radius blade shoulder arc, it is determined that the blade is mainly processed by milling and compound turning as the main process. The high-precision CNC machining center with five-axis milling and turning functions is the main machining equipment, and other auxiliary equipment includes cleaning machines, three-coordinate measuring machines, polishing machines, laser marking machines, thermal expansion meters, tool setting instruments, and code readers , balancing machine;
[0075] ②Exclude human factors and determine the storage and logistics transmission equipment required for the automation alternative of the process, including tower silos, robotic arms and truss guide rails, automatic loadi...
Embodiment 2
[0096] In order to meet the automatic processing, testing, grinding and polishing of 5 kinds of aero-engine compressor blades in the whole process at the same time, realize the self-adaptive control of production operation, realize the annual production capacity requirement of 35,000 blades, and the production demand of 90% pass rate , the automated line consists of 7 blade processing centers, 2 robotic grinding and polishing machines, 2 coordinate measuring machines, 2 sky rail robots, 2 automatic loading and unloading stations, 1 tower silo, and 2 pallet warehouses , 1 production system industrial computer, 1 CNC laser marking machine, 1 thermal expansion tester, 1 dynamic balancing machine, and 1 tool setting instrument (such as figure 1 , 2 shown).
[0097] The automatic movement link of the entire production line is the process of workpieces flowing between processes. The robotic hand picks up the workpiece from the silo, the robotic hand picks up the fixture from the fi...
PUM
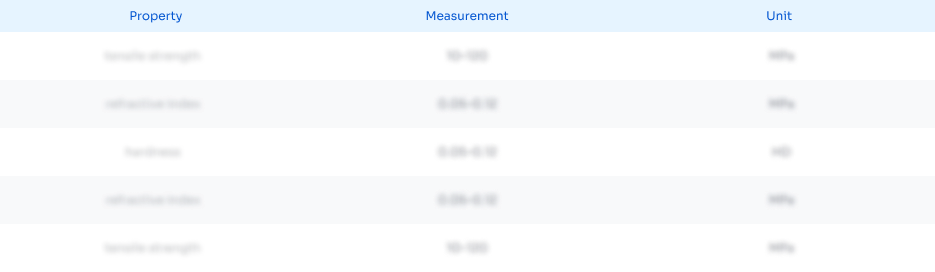
Abstract
Description
Claims
Application Information

- Generate Ideas
- Intellectual Property
- Life Sciences
- Materials
- Tech Scout
- Unparalleled Data Quality
- Higher Quality Content
- 60% Fewer Hallucinations
Browse by: Latest US Patents, China's latest patents, Technical Efficacy Thesaurus, Application Domain, Technology Topic, Popular Technical Reports.
© 2025 PatSnap. All rights reserved.Legal|Privacy policy|Modern Slavery Act Transparency Statement|Sitemap|About US| Contact US: help@patsnap.com