Forging method of relatively-large-size fine-grained austenitic gas valve steel SNCrW
A technology of austenitic and gas valve steel, which is applied in the forging field of large-scale fine-grained austenitic stainless steel SNCrW bars for gas valves. Problems such as fast precipitation speed, to achieve the effect of localization
- Summary
- Abstract
- Description
- Claims
- Application Information
AI Technical Summary
Problems solved by technology
Method used
Image
Examples
Embodiment 1
[0045] Produce SNCrW round steel with a size of Φ88mm.
[0046] 1. The smelting branch produces SNCrWΦ480mm electroslag ingots with qualified chemical composition;
[0047] 2. The electroslag ingot after high-temperature homogenization treatment is kept at 1200°C for 2 hours and then out of the furnace for forging;
[0048] 3. The fast forging machine performs upsetting operation, the upsetting reduction is 300mm, adopts the forging method at both ends, the 80mm reduction is drawn to a 450mm octagonal cross section, the end of the bottom pad is clamped, and the furnace is refired at 1200°C for 3 hours;
[0049] 4. The octagonal process of the quick forging machine is drawn to a 360mm octagonal section, of which the first pass is pressed to a ruler of 360mm, the second pass is 120mm to reduce the length, and the third and fourth passes are pressed to a ruler of 360mm. The pass is shaped according to the billet size of 360mm, and the final forging temperature of the corner is 9...
Embodiment 2
[0055] Produce SNCrW round steel with a size of Φ100mm.
[0056] 1. The smelting branch produces SNCrWΦ480mm electroslag ingots with qualified chemical composition;
[0057] 2. The electroslag ingot after high-temperature homogenization treatment is kept at 1210°C for 3 hours and then out of the furnace for forging;
[0058] 3. The fast forging machine performs upsetting operation, the upsetting reduction is 350mm, adopts the forging method at both ends, the 80mm reduction is drawn to a 450mm octagonal section, the end of the bottom pad is clamped, and the furnace is refired at 1200°C for 2.5 hours;
[0059] 4. The octagonal process of the quick forging machine is drawn to a 370mm octagonal cross-section, of which the first pass is pressed to a ruler of 370mm, the second pass is 120mm to reduce the length, and the third and fourth passes are pressed to a ruler of 370mm. The pass is shaped according to the billet size of 370mm, and the final forging temperature of the corner i...
Embodiment 3
[0065] Produce SNCrW round steel with a size of Φ115mm.
[0066] 1. The smelting branch produces SNCrWΦ480mm electroslag ingots with qualified chemical composition;
[0067] 2. The electroslag ingot after high-temperature homogenization treatment is kept at 1220°C for 4 hours and then out of the furnace for forging;
[0068] 3. The fast forging machine performs upsetting operation, the upsetting reduction is 350mm, adopts the forging method at both ends, the 80mm reduction is drawn to a 450mm octagonal section, the end of the bottom pad is clamped, and the furnace is refired at 1200°C for 2 hours;
[0069] 4. The octagonal process of the quick forging machine is drawn to a 380mm octagonal cross-section, of which the first pass is pressed to a ruler of 380mm, the second pass is 120mm to reduce the length, and the third and fourth passes are pressed to a ruler of 380mm. The pass is shaped according to the billet size of 380mm, the final forging temperature of the corner is 930°...
PUM
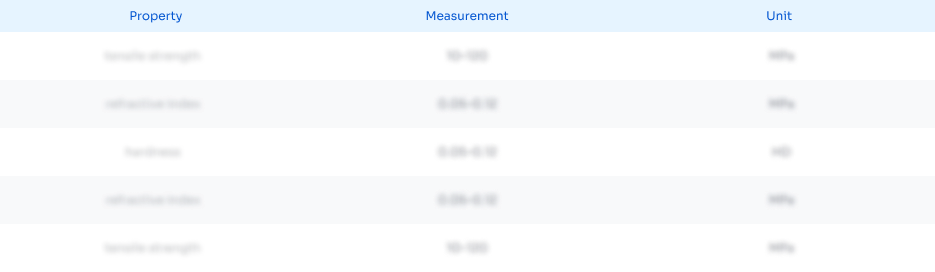
Abstract
Description
Claims
Application Information

- R&D
- Intellectual Property
- Life Sciences
- Materials
- Tech Scout
- Unparalleled Data Quality
- Higher Quality Content
- 60% Fewer Hallucinations
Browse by: Latest US Patents, China's latest patents, Technical Efficacy Thesaurus, Application Domain, Technology Topic, Popular Technical Reports.
© 2025 PatSnap. All rights reserved.Legal|Privacy policy|Modern Slavery Act Transparency Statement|Sitemap|About US| Contact US: help@patsnap.com