Supported rare earth-modified metal catalyst, and preparation method and application thereof
A metal catalyst and rare earth modification technology, which is applied in the direction of catalyst activation/preparation, metal/metal oxide/metal hydroxide catalyst, chemical instruments and methods, etc. In order to improve the selectivity of methyl mercaptan, increase the conversion rate of methanol and stabilize the impregnation solution
- Summary
- Abstract
- Description
- Claims
- Application Information
AI Technical Summary
Problems solved by technology
Method used
Image
Examples
Embodiment 1
[0045] Weigh 0.56g of lanthanum nitrate and dissolve it in 22g of deionized water, then add 40g of alumina carrier and impregnate for 6 hours, then dry at 80°C for 8 hours, and then bake at 450°C for 4 hours to make rare earth element modified oxide Aluminum carrier. The alumina carrier modified by the above-mentioned rare earth elements was impregnated in an alkali metal tungstate solution composed of 6.02g tungstic acid, 1.84g potassium hydroxide, 4.90g cesium hydroxide and 21g deionized water, and after 8 hours at 100 °C oven, and finally baked in a muffle furnace at 600 °C for 3 hours. The obtained catalyst La 2 o 3 content of 0.49%, alkali metal content of 9.89%, WO 3 The content is 19.56%.
Embodiment 2
[0047] Weigh 1.12g of lanthanum nitrate and dissolve it in 22g of deionized water, then add 40g of alumina support and impregnate for 6 hours, then dry at 80°C for 8 hours, and then bake at 450°C for 4 hours to make rare earth element modified oxide Aluminum carrier. The alumina carrier modified by the above rare earth elements was immersed in an alkali metal tungstate solution composed of 11.78g ammonium metatungstate, 2.46g potassium hydroxide, 3.68g cesium hydroxide and 21g deionized water. After 8 hours Dry it in an oven at 100°C, and finally heat it up to 600°C in a muffle furnace for 3 hours. The obtained catalyst La 2 o 3 content of 0.98%, alkali metal content of 8.15%, WO 3 The content is 19.68%.
Embodiment 3
[0049] Weigh 1.12g of cerium nitrate and dissolve it in 22g of deionized water, then add 40g of alumina carrier and impregnate for 6 hours, then dry at 80°C for 8 hours, and then bake at 450°C for 4 hours to make rare earth element-modified oxide Aluminum carrier. The alumina carrier modified by the above rare earth elements was immersed in an alkali metal tungstate solution composed of 11.78g ammonium metatungstate, 2.46g potassium hydroxide, 3.68g cesium hydroxide and 21g deionized water. After 8 hours Dry it in an oven at 100°C, and finally heat it up to 600°C in a muffle furnace for 3 hours. The obtained catalyst Ce 2 o 3 content of 0.95%, alkali metal content of 8.09%, WO 3 The content is 19.42%.
PUM
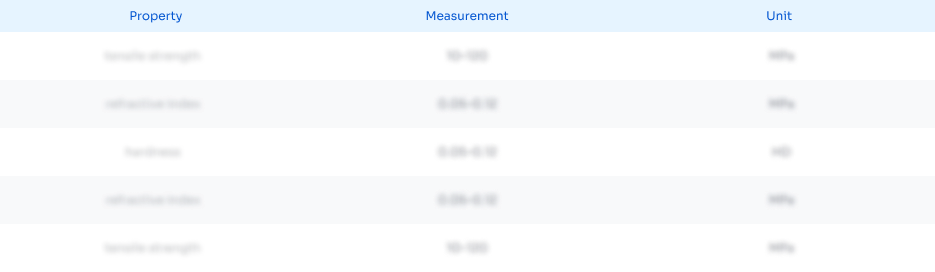
Abstract
Description
Claims
Application Information

- R&D
- Intellectual Property
- Life Sciences
- Materials
- Tech Scout
- Unparalleled Data Quality
- Higher Quality Content
- 60% Fewer Hallucinations
Browse by: Latest US Patents, China's latest patents, Technical Efficacy Thesaurus, Application Domain, Technology Topic, Popular Technical Reports.
© 2025 PatSnap. All rights reserved.Legal|Privacy policy|Modern Slavery Act Transparency Statement|Sitemap|About US| Contact US: help@patsnap.com