Sliding member and production method therefor
A sliding member and manufacturing method technology, applied in the directions of engine components, chemical instruments and methods, lubricating compositions, etc., can solve problems such as inability to reduce friction, and achieve the effects of improving fuel economy, promoting decomposition reaction, and being easy to form.
- Summary
- Abstract
- Description
- Claims
- Application Information
AI Technical Summary
Problems solved by technology
Method used
Image
Examples
Embodiment 1
[0041] (Example 1, Comparative Example 1)
[0042] As Example 1, a disk-shaped test piece made of bearing steel (SUJ2) was prepared, and a metal material containing Ti was used as a thermal spray material to perform atmospheric plasma spraying to form a thermal sprayed film 12 containing Ti. At this time, two types of metal powders are prepared for the thermal spray material, and a plurality of thermal spray films 12 are formed for each thermal spray material. The composition of the first type of metal powder of the thermal spray material was 100 mass % of Ti, and the composition of the second type of metal powder was 90 mass % of Ti, 6 mass % of aluminum (Al), and 4 mass % of vanadium (V). After each thermal spray film 12 is formed, polishing is performed to adjust the surface roughness of each thermal spray film 12 . Surface roughness is represented by the sum of payload roughness (Rk) and initial wear height (Rpk).
[0043] Each of the produced test pieces was subjected t...
Embodiment 2
[0048] As in Example 1, two types of thermal spray materials were used to form thermal spray films 12 on the test pieces, respectively. At this time, the amount of oxygen in the thermal spray film 12 was changed by changing the thermal spray output in five steps. The friction coefficient was examined in the same manner as in Example 1 for each of the produced test pieces. The result that can be obtained is Figure 4 shown in. like Figure 4 As shown, it was found that the smaller the amount of oxygen in the thermal spray coating 12, the lower the friction coefficient tends to be. If the oxygen amount in the thermal spray coating 12 is 10 mass % or less, the friction coefficient can be less than 0.04, which is preferable.
PUM
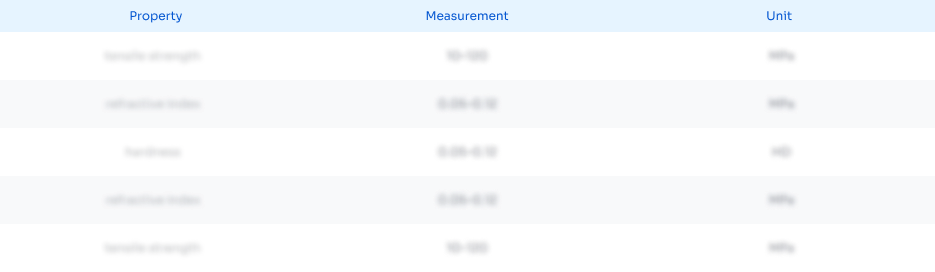
Abstract
Description
Claims
Application Information

- R&D
- Intellectual Property
- Life Sciences
- Materials
- Tech Scout
- Unparalleled Data Quality
- Higher Quality Content
- 60% Fewer Hallucinations
Browse by: Latest US Patents, China's latest patents, Technical Efficacy Thesaurus, Application Domain, Technology Topic, Popular Technical Reports.
© 2025 PatSnap. All rights reserved.Legal|Privacy policy|Modern Slavery Act Transparency Statement|Sitemap|About US| Contact US: help@patsnap.com