Wear-resistant and corrosion-resistant liner plate and preparation method thereof
A corrosion-resistant and liner technology, applied in the field of wear-resistant materials, can solve problems such as impact and collision between the body and the liner, machine damage, liner cracks, etc., to achieve the effects of increasing hardenability, saving energy, and improving service life
- Summary
- Abstract
- Description
- Claims
- Application Information
AI Technical Summary
Problems solved by technology
Method used
Examples
Embodiment 1
[0028] A method for preparing a wear-resistant and corrosion-resistant liner, comprising the following steps:
[0029] S1, add clean and dry ordinary steel scrap, pig iron, stainless steel scrap, magnesium ingot, ferromanganese, ferromolybdenum, nickel plate, titanium ingot, and waste electrode for carbon increase into the furnace, heat and melt, and adjust the composition to the percentage of each component For: carbon 1%, silicon 0.55%, magnesium 0.6%, manganese 0.55%, chromium 12%, molybdenum 1.6%, nickel 0.16%, titanium 0.16%, phosphorus 0.02%, sulfur 0.02%, the balance is iron, the temperature rises To 1550°C, add preheated ferrosilicon for precipitation deoxidation, 2 minutes before tapping the iron, use the method of deep insertion of aluminum wire for diffusion deoxidation, and then tap the iron;
[0030] S2, crush the sodium and cerium-based rare earths into small pieces with a particle size of less than 10mm, dry them at 280°C and place them at the bottom of the ladl...
Embodiment 2
[0033] A method for preparing a wear-resistant and corrosion-resistant liner, comprising the following steps:
[0034] S1, add clean and dry ordinary steel scrap, pig iron, stainless steel scrap, magnesium ingot, ferromanganese, ferromolybdenum, nickel plate, titanium ingot, and waste electrode for carbon increase into the furnace, heat and melt, and adjust the composition to the percentage of each component For: carbon 0.8%, silicon 0.8%, magnesium 0.7%, manganese 0.8%, chromium 11%, molybdenum 1.7%, nickel 0.14%, titanium 0.1%, phosphorus 0.06%, sulfur 0.06%, the balance is iron, the temperature rises To 1600°C, add preheated ferrosilicon for precipitation deoxidation, 2 minutes before tapping the iron, use the method of deep insertion of aluminum wire for diffusion deoxidation, and then tap the iron;
[0035] S2, crush sodium and cerium-based rare earths into small pieces with a particle size of less than 10mm, dry them at 280°C and place them at the bottom of the ladle, us...
Embodiment 3
[0038] A method for preparing a wear-resistant and corrosion-resistant liner, comprising the following steps:
[0039] S1, add clean and dry ordinary steel scrap, pig iron, stainless steel scrap, magnesium ingot, ferromanganese, ferromolybdenum, nickel plate, titanium ingot, and waste electrode for carbon increase into the furnace, heat and melt, and adjust the composition to the percentage of each component For: carbon 1%, silicon 0.4%, magnesium 0.4%, manganese 1.0%, chromium 13%, molybdenum 1.9%, nickel 0.1%, titanium 0.20%, phosphorus 0.04%, sulfur 0.04%, the balance is iron, the temperature rises To 1500°C, add preheated ferrosilicon for precipitation deoxidation, 2 minutes before tapping the iron, use the method of deep insertion of aluminum wire for diffusion deoxidation, and then tap the iron;
[0040] S2, crush potassium and cerium-based rare earths into small pieces with a particle size of less than 10mm, dry them at 280°C and place them at the bottom of the ladle, u...
PUM
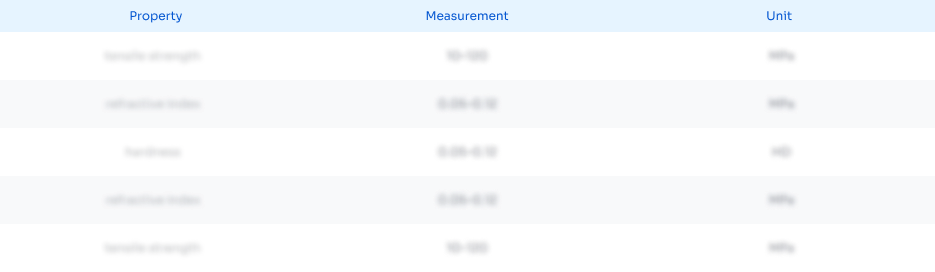
Abstract
Description
Claims
Application Information

- R&D
- Intellectual Property
- Life Sciences
- Materials
- Tech Scout
- Unparalleled Data Quality
- Higher Quality Content
- 60% Fewer Hallucinations
Browse by: Latest US Patents, China's latest patents, Technical Efficacy Thesaurus, Application Domain, Technology Topic, Popular Technical Reports.
© 2025 PatSnap. All rights reserved.Legal|Privacy policy|Modern Slavery Act Transparency Statement|Sitemap|About US| Contact US: help@patsnap.com