A green smelting method for recycled aluminum alloy
An aluminum alloy melt and aluminum alloy technology, applied in the field of recycled aluminum, can solve the problems of difficult disposal of refining slag, difficult control of melt composition, and white smoke pollution, etc., and achieve high utilization rate of argon gas, easy control, and high recovery rate Effect
- Summary
- Abstract
- Description
- Claims
- Application Information
AI Technical Summary
Problems solved by technology
Method used
Image
Examples
Embodiment 1
[0037] After smelting and adjusting the composition of the aluminum secondary resources after the paint removal, argon is used for refining and degassing at the same time, and the inclusions and hydrogen of the recycled aluminum alloy melt are removed. The argon gas is introduced through the breathable brick at the bottom of the melting furnace, and the recycled aluminum alloy melt is refined and degassed at 680°C for 120.0min, the flow rate of argon gas is 0.5L / min, the air pressure is 0.1MPa, and the average size of the bubbles is 0.5mm. The secondary aluminum alloy melt after refining and degassing has an inclusion content of 0.30%, a hydrogen content of 0.10ml / 100gAl, an aluminum ash residue composed of aluminum alloy and alumina, and does not contain salts and aluminum nitride pollution sources.
Embodiment 2
[0039] After smelting and adjusting the composition of the aluminum secondary resources after the paint removal, argon is used for refining and degassing at the same time, and the inclusions and hydrogen of the recycled aluminum alloy melt are removed. The argon gas is introduced through the breathable brick at the bottom of the melting furnace, and the recycled aluminum alloy melt is refined and degassed at 700°C for 110.0min, the flow rate of argon gas is 15.0L / min, the air pressure is 0.1MPa, and the average size of the bubbles is 2.0mm. The secondary aluminum alloy melt after refining and degassing has an inclusion content of 0.40%, a hydrogen content of 0.12ml / 100gAl, an aluminum ash residue composed of aluminum alloy and alumina, and does not contain salts and aluminum nitride pollution sources.
Embodiment 3
[0041] After smelting and adjusting the composition of the aluminum secondary resources after the paint removal, argon is used for refining and degassing at the same time, and the inclusions and hydrogen of the recycled aluminum alloy melt are removed. The argon gas is introduced through the breathable brick at the bottom of the melting furnace, and the recycled aluminum alloy melt is refined and degassed at 720°C for 100.0min, the flow rate of argon gas is 30.0L / min, the air pressure is 0.15MPa, and the average size of the bubbles is 4.0mm. The secondary aluminum alloy melt after refining and degassing has an inclusion content of 0.50%, a hydrogen content of 0.14ml / 100gAl, an aluminum ash residue composed of aluminum alloy and alumina, and does not contain salts and aluminum nitride pollution sources.
PUM
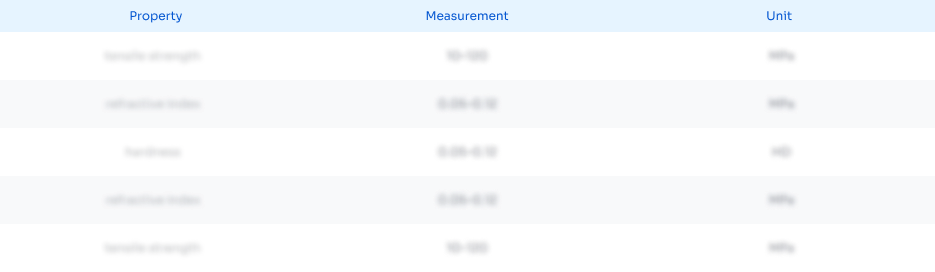
Abstract
Description
Claims
Application Information

- R&D
- Intellectual Property
- Life Sciences
- Materials
- Tech Scout
- Unparalleled Data Quality
- Higher Quality Content
- 60% Fewer Hallucinations
Browse by: Latest US Patents, China's latest patents, Technical Efficacy Thesaurus, Application Domain, Technology Topic, Popular Technical Reports.
© 2025 PatSnap. All rights reserved.Legal|Privacy policy|Modern Slavery Act Transparency Statement|Sitemap|About US| Contact US: help@patsnap.com