Garbage incineration waste heat boiler flue gas backflow system
A waste incineration and waste heat boiler technology, applied in incinerators, combustion methods, combustion types, etc., can solve problems such as unavoidable high-temperature corrosion, and achieve the effects of improving uneven velocity field, obvious scouring, and enhancing heat exchange.
- Summary
- Abstract
- Description
- Claims
- Application Information
AI Technical Summary
Problems solved by technology
Method used
Image
Examples
Embodiment Construction
[0024] The following will be described in more detail in conjunction with specific engineering cases, wherein the preferred embodiments of the present invention are described, it should be understood that those skilled in the art can modify the present invention described here and still achieve the beneficial effects of the present invention. Therefore, the following description should be understood as the broad knowledge of those skilled in the art, but not as a limitation of the present invention.
[0025] Case: Take a waste incineration waste heat boiler with a waste treatment capacity of 750t / d, a main steam parameter of 6.4MPa, and a temperature of 450°C as an example. After the flue gas at the tail of the boiler passes through the electrostatic precipitator 1, it passes through the electric inlet to adjust the damper 2, and part of the clean flue gas is extracted by the return fan 3, and the exit of the return fan 3 is arranged on the flue between the flue pipe box 7 in s...
PUM
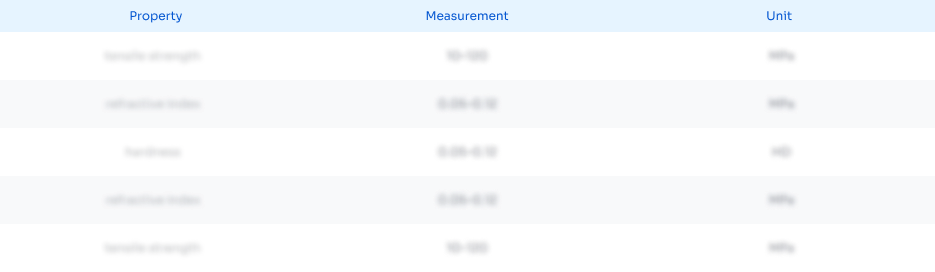
Abstract
Description
Claims
Application Information

- R&D
- Intellectual Property
- Life Sciences
- Materials
- Tech Scout
- Unparalleled Data Quality
- Higher Quality Content
- 60% Fewer Hallucinations
Browse by: Latest US Patents, China's latest patents, Technical Efficacy Thesaurus, Application Domain, Technology Topic, Popular Technical Reports.
© 2025 PatSnap. All rights reserved.Legal|Privacy policy|Modern Slavery Act Transparency Statement|Sitemap|About US| Contact US: help@patsnap.com