Granular double-layer reaction glaze and preparation method
A granular, reactive glaze technology, applied in the field of ceramic glaze, can solve problems such as affecting product benefits, affecting the overall decorative effect, and long firing time, and achieves the effects of short firing time, bright glaze, and low energy consumption
- Summary
- Abstract
- Description
- Claims
- Application Information
AI Technical Summary
Problems solved by technology
Method used
Image
Examples
Embodiment 1
[0047] Bottom glaze in parts by weight: 35 parts of albite powder, 8 parts of quartz powder, 8 parts of wollastonite powder, 4 parts of calcined alumina, 25 parts of kaolin, and 20 parts of dark brown. Surface glaze: 35 parts of high boron frit, 18 parts of quartz powder, 8 parts of wollastonite, 8 parts of spodumene, 12 parts of calcined zinc oxide, 10 parts of kaolin, 6 parts of calcined talc, 6 parts of titanium dioxide, zirconium silicate 8 servings. Add the above materials to the ball mill for ball milling, and then add water to the ball mill. The mass ratio of raw materials: balls: water is 1:2:0.6, and the ratio of large balls, medium balls and small balls in high alumina balls is 2:5 : 3 mass ratio, join in the ball mill, the ball milling time is 24h, the fineness of the glaze obtained after the ball milling is controlled at 0.05-0.08% of the 325 mesh sieve. After the glaze leaves the ball mill, pass through a 120-mesh sieve to obtain the glaze slurry, then measure th...
Embodiment 2
[0049] Bottom glaze in parts by weight: 40 parts of albite powder, 12 parts of quartz powder, 5 parts of wollastonite powder, 2 parts of calcined alumina, 26 parts of kaolin, and 15 parts of dark brown. Surface glaze: 40 parts of high boron frit, 13 parts of quartz powder, 10 parts of wollastonite, 5 parts of spodumene, 10 parts of calcined zinc oxide, 7 parts of kaolin, 5 parts of calcined talc, 6 parts of titanium dioxide, zirconium silicate 8 servings. Add the above materials to the ball mill for ball milling, and then add water to the ball mill. The mass ratio of raw materials: balls: water is 1:2:0.6, and the ratio of large balls, medium balls and small balls in high alumina balls is 2:5 : 3 mass ratio, join in the ball mill, the ball milling time is 24h, the fineness of the glaze obtained after the ball milling is controlled at 0.1-0.12% of the 325 mesh sieve. After the glaze leaves the ball mill, pass through a 120-mesh sieve to obtain the glaze slurry, then measure th...
Embodiment 3
[0051] Bottom glaze in parts by weight: 30 parts of albite powder, 12 parts of quartz powder, 5 parts of wollastonite powder, 6 parts of calcined alumina, 25 parts of kaolin, and 24 parts of dark brown. Surface glaze: 45 parts of high boron frit, 15 parts of quartz powder, 5 parts of wollastonite, 11 parts of spodumene, 10 parts of calcined zinc oxide, 7 parts of kaolin, 5 parts of calcined talc, 6 parts of titanium dioxide, zirconium silicate 8 servings. Add the above materials to the ball mill for ball milling, and then add water to the ball mill. The mass ratio of raw materials: balls: water is 1:2:0.6, and the ratio of large balls, medium balls and small balls in high alumina balls is 2:5 : 3 mass ratio, join in the ball mill, the ball milling time is 24h, the fineness of the glaze obtained after the ball milling is controlled at 0.08-0.12% of the 325 mesh sieve. After the glaze comes out of the ball mill, pass through a 120-mesh sieve to obtain the glaze slurry, then mea...
PUM
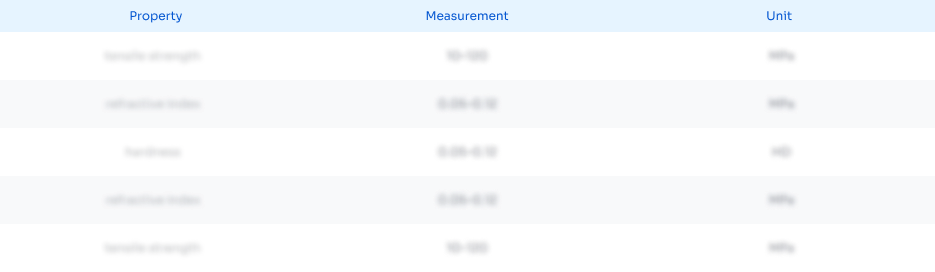
Abstract
Description
Claims
Application Information

- R&D
- Intellectual Property
- Life Sciences
- Materials
- Tech Scout
- Unparalleled Data Quality
- Higher Quality Content
- 60% Fewer Hallucinations
Browse by: Latest US Patents, China's latest patents, Technical Efficacy Thesaurus, Application Domain, Technology Topic, Popular Technical Reports.
© 2025 PatSnap. All rights reserved.Legal|Privacy policy|Modern Slavery Act Transparency Statement|Sitemap|About US| Contact US: help@patsnap.com