Displacement testing system and displacement testing method
A test system and test method technology, applied in the test field, can solve problems such as circumferential displacement measurement failure, product reprocessing, and product destructiveness, and achieve low product destructiveness, strong sense of reality, and simple and easy operation Effect
- Summary
- Abstract
- Description
- Claims
- Application Information
AI Technical Summary
Problems solved by technology
Method used
Image
Examples
Embodiment Construction
[0049] The present invention will be further described below in conjunction with accompanying drawing:
[0050] Such as figure 1 shown;
[0051] Displacement testing system, including:
[0052] Centrifuge; the centrifuge includes a hanging basket 1, a centrifuge arm 10, and a main shaft 11, and the test product is placed in the hanging basket 1; the outer wall of the test product is provided with openings;
[0053] A micro-fiber probe 5; one end of the micro-fiber probe 5 is placed in the opening of the test product;
[0054] The mounting bracket 6, the micro-fiber probe 5 is also fixed on the mounting bracket 6;
[0055] Feature point calibration label 3; feature point calibration label 3 is set on the upper structure and lower structure of the test product;
[0056] The micro-fiber insertion part 7; the micro-fiber insertion part 7 is fixedly installed along the centrifuge arm; and protective measures are taken;
[0057] Imaging and image acquisition equipment 13;
[0...
PUM
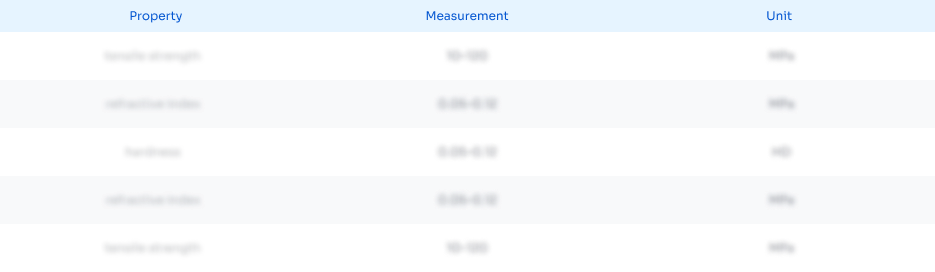
Abstract
Description
Claims
Application Information

- R&D Engineer
- R&D Manager
- IP Professional
- Industry Leading Data Capabilities
- Powerful AI technology
- Patent DNA Extraction
Browse by: Latest US Patents, China's latest patents, Technical Efficacy Thesaurus, Application Domain, Technology Topic, Popular Technical Reports.
© 2024 PatSnap. All rights reserved.Legal|Privacy policy|Modern Slavery Act Transparency Statement|Sitemap|About US| Contact US: help@patsnap.com