Method for preparing glass fiber reinforced nylon through in-situ polymerization, glass fiber reinforced nylon prepared by method
An in-situ polymerization and glass fiber technology, which is applied in the field of glass fiber reinforced nylon, can solve the problems of secondary pollution, expensive processing of copper shell water meters, etc., and achieve the goals of reducing water absorption, improving "floating fiber" problems, and excellent hydrolysis resistance Effect
- Summary
- Abstract
- Description
- Claims
- Application Information
AI Technical Summary
Problems solved by technology
Method used
Image
Examples
Embodiment 1
[0022] Embodiment 1: Add 90 parts by weight of caprolactam, 10 parts by weight of glass fibers, 10 parts by weight of water, 0.5 parts by weight of phosphorous acid, 0.3 parts by weight of 1098 antioxidant in a stainless steel reactor with jacketed coil pipe and agitator , 3 parts by weight of polyolefin thermoplastic elastomer, 0.2 parts by weight of silicone powder and 0.5 parts by weight of polycarbodiimide. ① Check the airtightness of the reactor, vacuumize and replace the air in the reactor with high-purity inert gas, and try to control the oxygen content in the reactor below 0.005wt%. ②Salt formation: raise the temperature to 90°C, and react under this condition for 1h to carry out the salt formation reaction; ③Prepolymerization: After completing the salt formation stage, raise the temperature to 190°C, and react for 3h at a pressure of 0.6MPa. ④ Final polymerization: After the prepolymerization stage is completed, the temperature is raised to 250°C, and the pressure is ...
Embodiment 2
[0023] Embodiment 2: Add 80 parts by weight of caprolactam, 20 parts by weight of glass fibers, 10 parts by weight of water, 0.5 parts by weight of phosphorous acid, 0.3 parts by weight of 1098 antioxidant in the stainless steel reactor with jacketed coil pipe and stirrer , 3 parts by weight of polyolefin thermoplastic elastomer, 0.2 parts by weight of silicone powder and 0.5 parts by weight of polycarbodiimide. ① Check the airtightness of the reactor, vacuumize and replace the air in the reactor with high-purity inert gas, and try to control the oxygen content in the reactor below 0.005wt%. ②Salt formation: raise the temperature to 90°C, and react under this condition for 1h to carry out the salt formation reaction; ③Prepolymerization: After completing the salt formation stage, raise the temperature to 190°C, and react for 3h at a pressure of 0.6MPa. ④ Final polymerization: After the prepolymerization stage is completed, the temperature is raised to 250°C, and the pressure is...
Embodiment 3
[0024] Embodiment 3: Add 70 parts by weight of caprolactam, 30 parts by weight of glass fibers, 10 parts by weight of water, 0.5 parts by weight of phosphorous acid, 0.3 parts by weight of 1098 antioxidant in the stainless steel reactor with jacketed coil pipe and stirrer , 3 parts by weight of polyolefin thermoplastic elastomer, 0.2 parts by weight of silicone powder and 0.5 parts by weight of polycarbodiimide. ① Check the airtightness of the reactor, vacuumize and replace the air in the reactor with high-purity inert gas, and try to control the oxygen content in the reactor below 0.005wt%. ②Salt formation: raise the temperature to 90°C, and react under this condition for 1h to carry out the salt formation reaction; ③Prepolymerization: After completing the salt formation stage, raise the temperature to 190°C, and react for 3h at a pressure of 0.6MPa. ④ Final polymerization: After the prepolymerization stage is completed, the temperature is raised to 250°C, and the pressure is...
PUM
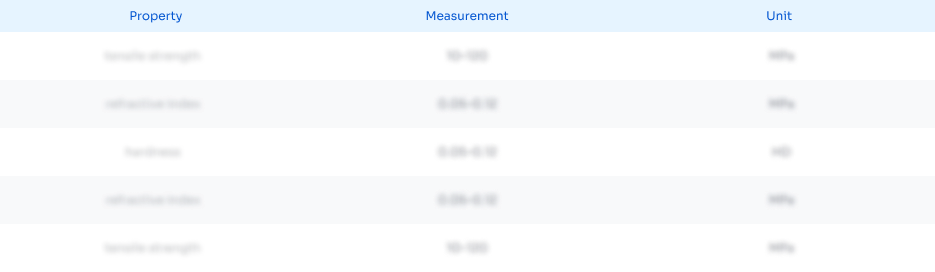
Abstract
Description
Claims
Application Information

- R&D Engineer
- R&D Manager
- IP Professional
- Industry Leading Data Capabilities
- Powerful AI technology
- Patent DNA Extraction
Browse by: Latest US Patents, China's latest patents, Technical Efficacy Thesaurus, Application Domain, Technology Topic, Popular Technical Reports.
© 2024 PatSnap. All rights reserved.Legal|Privacy policy|Modern Slavery Act Transparency Statement|Sitemap|About US| Contact US: help@patsnap.com