Ether-ester copolymerization viscosity-reduction-type polycarboxylate superplasticizer and preparation method thereof
A technology of viscous polycarboxylic acid and water reducing agent, applied in the field of building admixtures, can solve problems such as limitation of wide use, and achieve the effects of improving steric hindrance, improving bleeding, and simple preparation process
- Summary
- Abstract
- Description
- Claims
- Application Information
AI Technical Summary
Problems solved by technology
Method used
Image
Examples
Embodiment 1
[0031] (1) Take each raw material component by the following parts by weight: 70 parts by weight of 4-hydroxybutyl vinyl polyoxyethylene base ether (VPEG molecular weight 4000), 40 parts by weight of methoxy polyethylene glycol methacrylate, 8 parts by weight of acrylic acid, 6 parts by weight of hydroxyethyl acrylate, 2 parts by weight of 4-(1-carboxyvinyl) benzoic acid, 2 parts by weight of unsaturated highly branched small monomers, 0.5 parts by weight of hydrogen peroxide, triacetoxy 0.7 parts by weight of sodium borohydride, 0.35 parts by weight of 3-mercaptoacetic acid-2-methylhexyl ester, 4 parts by weight of potassium hydroxide aqueous solution of 50wt%, 5 parts by weight of aqueous sodium hydroxide solution of 32wt%, and the rest are deionized water , adjusted to 50% solid content.
[0032] (2) Dissolve acrylic acid and 2-methylhexyl 3-mercaptoacetate in 15 parts by weight of deionized water, and adjust the pH to 5.5 to 6.0 with 50 wt % potassium hydroxide aqueous sol...
Embodiment 2
[0037] (1) Weigh 60 parts by weight of each raw material component 4-hydroxybutyl vinyl polyoxyethylene base ether (VPEG molecular weight 4500), 50 parts by weight of methoxypolyethylene glycol methacrylate, acrylic acid 6 parts by weight, 3 parts by weight of hydroxyethyl methacrylate, 3 parts by weight of 4-(1-carboxyvinyl) benzoic acid, 1 part by weight of unsaturated highly branched small monomer, 0.6 parts by weight of sodium persulfate, dihydrochloric acid 0.8 parts by weight of hydrazine, 0.4 parts by weight of 3-mercaptoacetic acid-2-methylhexyl ester, 2 parts by weight of potassium hydroxide aqueous solution of 50wt%, 6 parts by weight of aqueous sodium hydroxide solution of 32wt%, all the other are deionized water, adjusted to 50% solids.
[0038] (2) Dissolve acrylic acid and 2-methylhexyl 3-mercaptoacetate in 15 parts by weight of deionized water, and adjust the pH to 5.5 to 6.0 with 50 wt % potassium hydroxide aqueous solution to obtain the first solution; hydrazi...
Embodiment 3
[0043] (1) Take each raw material component by the following parts by weight: 80 parts by weight of 4-hydroxybutyl vinyl polyoxyethylene base ether (VPEG molecular weight 6000), 25 parts by weight of methoxy polyethylene glycol methacrylate, 7 parts by weight of methacrylic acid, 3 parts by weight of hydroxypropyl acrylate, 5 parts by weight of 4-(1-carboxyvinyl) benzoic acid, 3 parts by weight of unsaturated highly branched small monomers, 0.4 parts by weight of ammonium persulfate, three parts by weight 0.7 parts by weight of sodium acetoxy borohydride, 0.5 parts by weight of 2,4-diphenyl-4-methyl-1-pentene, 3 parts by weight of 50 wt % potassium hydroxide aqueous solution, 32 wt % sodium hydroxide aqueous solution 4 parts by weight, and the rest is deionized water, which is adjusted to 50% solid content.
[0044] (2) Dissolve methacrylic acid and 2,4-diphenyl-4-methyl-1-pentene in 15 parts by weight of deionized water, and adjust the pH to 5.5 to 6.0 with 50 wt % potassium ...
PUM
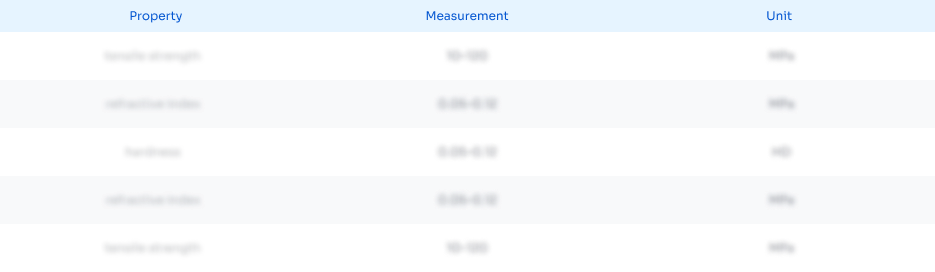
Abstract
Description
Claims
Application Information

- R&D
- Intellectual Property
- Life Sciences
- Materials
- Tech Scout
- Unparalleled Data Quality
- Higher Quality Content
- 60% Fewer Hallucinations
Browse by: Latest US Patents, China's latest patents, Technical Efficacy Thesaurus, Application Domain, Technology Topic, Popular Technical Reports.
© 2025 PatSnap. All rights reserved.Legal|Privacy policy|Modern Slavery Act Transparency Statement|Sitemap|About US| Contact US: help@patsnap.com