A 2D laser positioning method for train body doors and windows
A laser positioning and car body technology, applied in the field of physics, can solve the problem of low precision of train window assembly and end wall drilling, and achieve the effects of high layout design flexibility, high algorithm robustness, and high result reliability.
- Summary
- Abstract
- Description
- Claims
- Application Information
AI Technical Summary
Problems solved by technology
Method used
Image
Examples
Embodiment 1
[0078] like figure 2 As shown, the equipment used in a 2D laser positioning method for doors and windows of a train body of the present invention includes an AGV car (automatic guided transport vehicle) 1 and a manipulator 2, and the manipulator 2 is arranged on the automatic guided transport vehicle 1 Above, the end of the manipulator 2 is also provided with a fixture 7, the fixture 7 is fixedly provided with a 2D laser sensor 3, the fixture 7 is also provided with an operating tool 4, and the 2D laser sensor 3 is connected with a computer 8, the manipulator 2 is connected with a controller 9, and the controller 9 is connected with the computer 8.
[0079] Further, the automatic guided transport vehicle 1 is manually driven to one of the window frames 5 of the vehicle body 6, and the tool 7 on the manipulator 2 is controlled by means of teaching to install or process the window frame 5, Save the installation and processing track, use the teaching method to control the 2D la...
Embodiment 2
[0082] like Figure 5 As shown, the present invention provides a 2D laser positioning method for doors and windows of a train body, comprising the following steps:
[0083] 1) A process of calibrating the window frame of the door and window of the train body using the device of Embodiment 1, the described process of calibrating the window frame of the door and window of the train body is: manually control the automatic guided transport vehicle to reach a pair of trains. The position where the window frame of the door and window of the car body is roughly positioned; the center of the door and window frame of the train body is set as the origin of the base coordinate of the manipulator (the method of the present invention is not sensitive to the selection of the center point, and the error within 10mm is allowed), showing Teach the manipulator, use the operating tool on the end of the manipulator to install or process the window frame 5 of the car body, and save the installatio...
PUM
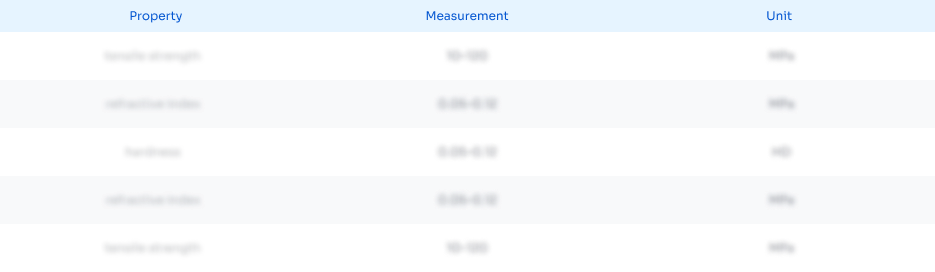
Abstract
Description
Claims
Application Information

- R&D
- Intellectual Property
- Life Sciences
- Materials
- Tech Scout
- Unparalleled Data Quality
- Higher Quality Content
- 60% Fewer Hallucinations
Browse by: Latest US Patents, China's latest patents, Technical Efficacy Thesaurus, Application Domain, Technology Topic, Popular Technical Reports.
© 2025 PatSnap. All rights reserved.Legal|Privacy policy|Modern Slavery Act Transparency Statement|Sitemap|About US| Contact US: help@patsnap.com