2D (two-dimensional) laser positioning method of door and window on train body of train
A laser positioning and car body technology, applied in the field of physics, can solve the problems of low accuracy of train window assembly and end wall drilling
- Summary
- Abstract
- Description
- Claims
- Application Information
AI Technical Summary
Problems solved by technology
Method used
Image
Examples
Embodiment 1
[0078] Such as figure 2 As shown, the equipment used in the 2D laser positioning method for doors and windows of a train body in the present invention includes an AGV trolley (automatic guided transport vehicle) 1 and a manipulator 2, and the manipulator 2 is arranged on the automatic guided transport vehicle 1 Above, the end of the manipulator 2 is also provided with a clamp 7, the clamp 7 is fixedly provided with a 2D laser sensor 3, and the clamp 7 is also provided with an operating tool 4, and the 2D laser sensor 3 is connected with a computer 8, and the manipulator 2 is connected with a controller 9, and the controller 9 is connected with the computer 8.
[0079] Further, the automatic guided transport vehicle 1 is manually driven to one of the window frames 5 of the car body 6, and the tool 7 on the manipulator 2 is controlled by a teaching method to install or process the window frame 5, Save the installation and processing track, use the teaching method to control th...
Embodiment 2
[0082] Such as Figure 5 As shown, the present invention provides a 2D laser positioning method for train body doors and windows, comprising the following steps:
[0083] 1) A process of calibrating the window frame of the train body door and window using the device of embodiment 1, the described process of calibrating the window frame of the train body door and window is: manually controlling the automatic guided transport vehicle to arrive at a pair of train The position where the window frame of the car body door and window is roughly positioned; the center of the door window frame of the train car body is set as the manipulator base coordinate origin (the method of the present invention is insensitive to the selection of the center point, allowing an error within 10mm), as shown Teach the manipulator, use the operating tool on the end of the manipulator to install or process the window frame 5 of the car body, and save the installation and processing track;
[0084] 2) Ke...
PUM
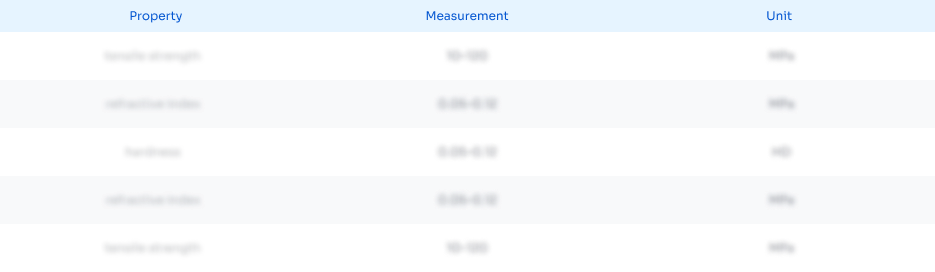
Abstract
Description
Claims
Application Information

- R&D Engineer
- R&D Manager
- IP Professional
- Industry Leading Data Capabilities
- Powerful AI technology
- Patent DNA Extraction
Browse by: Latest US Patents, China's latest patents, Technical Efficacy Thesaurus, Application Domain, Technology Topic, Popular Technical Reports.
© 2024 PatSnap. All rights reserved.Legal|Privacy policy|Modern Slavery Act Transparency Statement|Sitemap|About US| Contact US: help@patsnap.com