Cement kiln flue gas denitration process
A cement kiln and denitrification technology, which is applied in the direction of gas treatment, dispersed particle separation, membrane technology, etc., can solve the problems of flue gas backflow, secondary pollution, and low denitration efficiency, so as to increase the processing capacity, increase time, and improve The effect of denitrification effect
- Summary
- Abstract
- Description
- Claims
- Application Information
AI Technical Summary
Problems solved by technology
Method used
Image
Examples
Embodiment 1
[0026] A cement kiln flue gas denitrification process, comprising the following steps:
[0027] Step 1: Mix vanadium-titanium slag, biomass carbon powder, cement raw meal, foaming agent, and water with masses of 2kg, 8kg, 30kg, 1kg, and 20kg respectively, and pour to form a denitrification cylinder 1, which is round Cylindrical, wherein the particle size of the biomass carbon powder is 0.02mm, and pores are formed on the wall of the denitrification cylinder 1;
[0028] Step 2: If figure 1 , 2 As shown, the lower part of the denitrification tower 2 is fixedly installed on the frame by bolts, and the bottom of the denitrification tower 2 is provided with a leakage port, and the bottom of the denitrification tower 2 is slidably provided with a baffle 3 for sealing the leakage port; The upper part of the tower 2 is in the shape of a cuboid, and the rotating tube 4 is installed horizontally in the denitrification tower 2, such as figure 2 As shown, after the rotating pipe 4 pen...
Embodiment 2
[0034] In order to solve the problem that there is no need to stop the kiln when replacing the denitrification cylinder 1, on the basis of embodiment 1, the denitrification tower 2 of embodiment 2 is also provided with a broken cylinder pouring mechanism. The broken cylinder pouring mechanism includes a broken cylinder unit and a pouring unit. In step 2 of Example 1, after the denitration cylinder 1 has been used for a period of time, the cylinder breaking unit can break the denitration cylinder 1 in the denitration tower 2, and the pouring unit can pour in the denitration tower 2 to form a new denitration cylinder 1.
[0035] Specifically, such as figure 2 As shown, the pouring unit includes a pouring port 6 and a casing 7, the left end of the casing 7 is sealed, the casing 7 runs through the left side wall of the denitrification tower 2 and is rotatably connected with the left side wall of the denitrification tower 2, and the left end of the casing 7 passes through the The ...
PUM
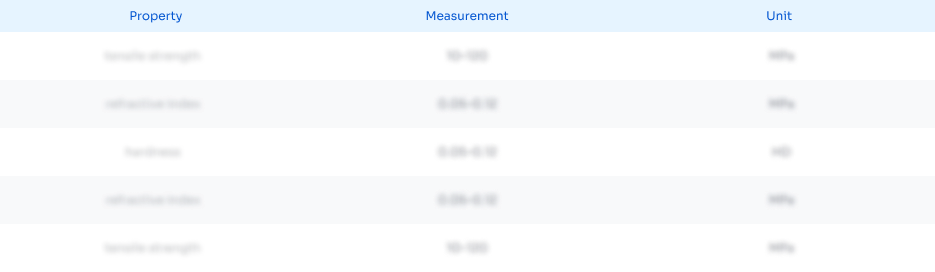
Abstract
Description
Claims
Application Information

- R&D Engineer
- R&D Manager
- IP Professional
- Industry Leading Data Capabilities
- Powerful AI technology
- Patent DNA Extraction
Browse by: Latest US Patents, China's latest patents, Technical Efficacy Thesaurus, Application Domain, Technology Topic, Popular Technical Reports.
© 2024 PatSnap. All rights reserved.Legal|Privacy policy|Modern Slavery Act Transparency Statement|Sitemap|About US| Contact US: help@patsnap.com