Topological optimization design method of friction stir welding robot base structure
A technology of robot base and friction stir welding, which is applied in the directions of instruments, calculations, and electrical digital data processing, etc., can solve the problems of welding position deviation, welding equipment structure deformation, and affecting welding quality, etc., to achieve improved dynamic performance and light overall quality Effect
- Summary
- Abstract
- Description
- Claims
- Application Information
AI Technical Summary
Problems solved by technology
Method used
Image
Examples
Embodiment Construction
[0045] The present invention will be described in further detail below in conjunction with the accompanying drawings.
[0046] Such as figure 1 As shown, the welding body part of the friction stir welding robot includes a base 1, a column 2, a ram 3, a turntable 4 and other structures, wherein the column 2 as the Y axis is located between the base 1 of the X axis and the ram 3 of the Z axis. Since the column 2 has many connection positions with other large components, its loading situation is relatively complicated. The two ends are also connected to the saddle 5 on the ram 3 through the guide rail slider pair 6 and the ball screw pair, and the above connection structures are known technologies in the art.
[0047] Such as figure 2As shown, the structure of the base 1 mainly includes internal ribs 104, sand outlet holes 105, external guide rails 101, anchor bolt mounting frames 107, hoisting holes 106, screw mounting seats 102, grating rulers 103, travel switches 108 and ot...
PUM
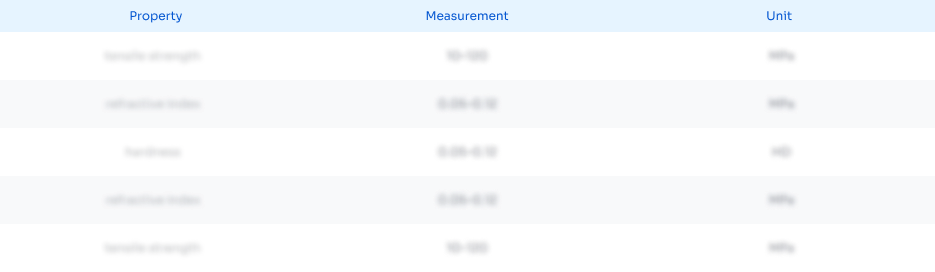
Abstract
Description
Claims
Application Information

- R&D Engineer
- R&D Manager
- IP Professional
- Industry Leading Data Capabilities
- Powerful AI technology
- Patent DNA Extraction
Browse by: Latest US Patents, China's latest patents, Technical Efficacy Thesaurus, Application Domain, Technology Topic, Popular Technical Reports.
© 2024 PatSnap. All rights reserved.Legal|Privacy policy|Modern Slavery Act Transparency Statement|Sitemap|About US| Contact US: help@patsnap.com