HDI printed circuit board manufacturing method and HDI printed circuit board
A printed circuit board and manufacturing method technology, applied in printed circuit manufacturing, printed circuits, printed circuit components and other directions, can solve problems such as poor layered foaming, reduce manufacturing cycles, increase wiring area, and improve manufacturing yields Effect
- Summary
- Abstract
- Description
- Claims
- Application Information
AI Technical Summary
Problems solved by technology
Method used
Image
Examples
Embodiment 1
[0036] Embodiment 1 provides a kind of manufacturing method of HDI printed circuit board, and this method comprises the following steps:
[0037] S1: core board pretreatment step;
[0038] S2: Pressing and graphic transfer steps; intermediate processing steps are included between the pressing and graphic transfer steps;
[0039] S3: graphic electroplating step;
[0040] S4: post-processing step.
[0041] In step S1, the core board pretreatment step includes material cutting and inner-layer circuit fabrication, and the inner-layer circuit fabrication is to fabricate L5 and L6 layer circuits.
[0042] Step S2 actually includes all the intermediate processing steps between each pressing step and graphic transfer step and the corresponding pressing step and graphic transfer step;
[0043] The pressing steps include the first pressing step, the second pressing step, the third pressing step and the fourth pressing step; the pattern transfer step includes the first graphic transfe...
Embodiment 2
[0077] Embodiment 2 is provided based on Embodiment 1, and its difference is:
[0078] In step S211, the copper of the circuit board after the pressing step is reduced to a copper thickness of 9 μm;
[0079] In step S214, the resin plug hole is to fill the hole with non-insulating resin, so that the hole becomes a whole, which can increase the wiring and increase the function design of the hole; the plug hole adopts a special plug resin printing machine equipment Production, plugging speed: 200mm / min; front ink pressure: 1.8bar, rear ink pressure: 4.0bar, baking before plugging, among which baking plate parameters: 100°C / 40min, baking plate parameters after plugging: 110°C / 40min, after the hole is plugged, the protruding resin is smoothed with a grinding machine.
Embodiment 3
[0081] Embodiment 3 is provided based on Embodiment 1, and its difference is:
[0082] In step S211, the copper of the circuit board after the pressing step is reduced to a copper thickness of 10 μm;
[0083] In step S214, the resin plug hole is to fill the hole with non-insulating resin, so that the hole becomes a whole, which can increase the wiring and increase the function design of the hole; the plug hole adopts a special plug resin printing machine equipment Production, plugging speed: 200mm / min; front ink pressure: 1.8bar, rear ink pressure: 4.0bar, baking before plugging, among which the baking plate parameter: 100℃ / 40min, the baking plate parameter after plugging: 150℃ / 60min, after the hole is plugged, the protruding resin is smoothed with a grinding machine.
PUM
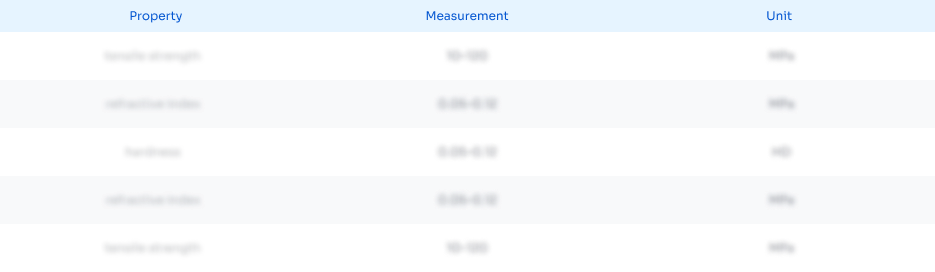
Abstract
Description
Claims
Application Information

- Generate Ideas
- Intellectual Property
- Life Sciences
- Materials
- Tech Scout
- Unparalleled Data Quality
- Higher Quality Content
- 60% Fewer Hallucinations
Browse by: Latest US Patents, China's latest patents, Technical Efficacy Thesaurus, Application Domain, Technology Topic, Popular Technical Reports.
© 2025 PatSnap. All rights reserved.Legal|Privacy policy|Modern Slavery Act Transparency Statement|Sitemap|About US| Contact US: help@patsnap.com