Method for improving Fe content allowedness of high-strong and high-toughness aluminum alloy for automobile structural part
A technology for aluminum alloys and structural parts, applied in the field of aluminum alloys, can solve the problems of difficulty in stirring Fe phase uniformly, increase the preparation cost of aluminum-silicon alloys, etc., and achieve the effects of easy recycling, low cost, and easy recycling.
- Summary
- Abstract
- Description
- Claims
- Application Information
AI Technical Summary
Problems solved by technology
Method used
Image
Examples
Embodiment 1
[0040] According to the mass percentage Mg: 0.2%, Si: 9.0%, Mn: 0.4%, Fe: 0.25%, Ti: 0.05%, Zn: 0.05%, Cu: 0.02%, Sr: 0.006%, the balance is Al alloy and Carry out smelting, add Al-Sr master alloy according to the Sr yield of 0.006% at 730 ° C, and pass argon gas into the melt at 710 ° C ~ 720 ° C for 10 minutes. After passing the argon gas, perform ultrasonic vibration Treatment, the vibration time is 3min, the frequency of ultrasonic vibration is 20-80kHz, the aluminum alloy melt is obtained after the vibration stops, the obtained aluminum alloy is die-casted, the casting temperature is 680°C, and the aluminum alloy is solid solution treated at 480°C for 5h, After water quenching, aging treatment at 170°C for 6 hours, the metallographic structure is as follows figure 2 shown.
Embodiment 2
[0042] According to mass percentage Mg: 0.2%, Si: 9.0%, Mn: 0.4%, Fe: 0.25%, Ti: 0.05%, Zn: 0.05%, Cu: 0.02%, Ce+La mixed rare earth: 0.1%, Sr: 0.006 %, the balance is Al to prepare the alloy and smelt it. When the melting temperature is ≥760°C, add Ce+La mixed rare earth to the melt, and press the mixed rare earth into the alloy liquid and stir evenly. When the temperature is 730°C, press The yield of Sr is 0.006% and Al-Sr master alloy is added. When the melt is 710℃~720℃, argon gas is introduced for 10 minutes. After the argon gas is passed, ultrasonic vibration treatment is carried out. The frequency of vibration is 20-80kHz. After the vibration stops, the aluminum alloy melt is obtained, and the obtained aluminum alloy is die-casted. The casting temperature is 680°C. The aluminum alloy is solid solution treated at 480°C for 5h, and after water quenching, it is aged at 170°C. Treated for 6h, its metallographic structure is as follows image 3 As shown, in order to compare...
Embodiment 3
[0044] According to mass percentage Mg: 0.3%, Si: 10.0%, Mn: 0.3%, Fe: 0.35%, Ti: 0.05%, Zn: 0.07%, Cu: 0.03%, Ce+La mixed rare earth: 0.30%, Sr: 0.01 %, the balance is Al sample preparation and smelting. When the melting temperature is ≥760°C, add Ce+La mixed rare earth to the melt, and press the mixed rare earth into the alloy liquid and stir evenly. When the temperature is 730°C, press The yield of Sr is 0.01% and Al-Sr master alloy is added. When the melt is 710 ℃ ~ 720 ℃, argon is introduced. The time of argon is 10 minutes. The time is 3 minutes, the frequency of ultrasonic vibration is 20-80kHz, after the vibration stops, the aluminum alloy melt is obtained, the obtained aluminum alloy is die-casted, the casting temperature is 680°C, the aluminum alloy is solution treated at 500°C for 4h, and after water quenching , aged at 180°C for 4h.
PUM
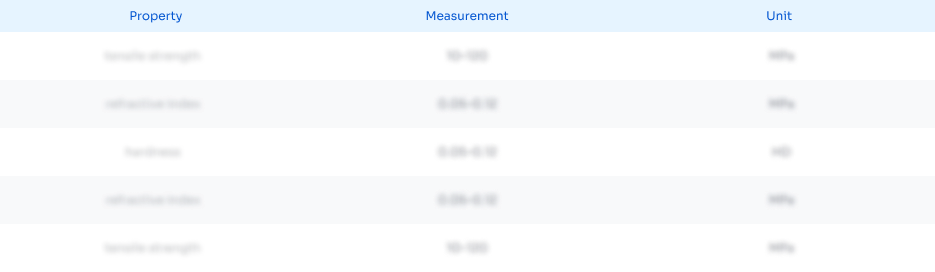
Abstract
Description
Claims
Application Information

- R&D
- Intellectual Property
- Life Sciences
- Materials
- Tech Scout
- Unparalleled Data Quality
- Higher Quality Content
- 60% Fewer Hallucinations
Browse by: Latest US Patents, China's latest patents, Technical Efficacy Thesaurus, Application Domain, Technology Topic, Popular Technical Reports.
© 2025 PatSnap. All rights reserved.Legal|Privacy policy|Modern Slavery Act Transparency Statement|Sitemap|About US| Contact US: help@patsnap.com