A kind of preparation method and die-casting method of anodic oxidation die-casting aluminum alloy material
A casting aluminum alloy, anodizing technology, applied in the field of aluminum alloy materials, can solve the problems of poor fluidity of aluminum liquid, anodic oxidation, poor effect, etc., and achieve the effect of good die-casting forming performance
- Summary
- Abstract
- Description
- Claims
- Application Information
AI Technical Summary
Problems solved by technology
Method used
Image
Examples
preparation example Construction
[0025] An embodiment of the present invention provides a method for preparing an anodizable die-casting aluminum alloy material, which is characterized in that it includes the following steps:
[0026] (1) Put in 80%-90% aluminum ingots first, and when the temperature rises to 850°C-880°C, add manganese element additives and titanium element additives; preferably when the temperature rises to 860°C-880°C, put in manganese element additives, titanium element additives additive.
[0027] (2) Put in the remaining aluminum ingots, lower the temperature of the molten aluminum and control it at 740°C-780°C, and add a sodium-free refining agent for refining and purification;
[0028] (3) sampling test;
[0029] (4) When the composition of the metal solution is within the following range: Si≤0.2%, Fe≤0.2%, Cu≤0.3%, Mn is 0.5%-2%, Mg≤0.3%, Zn≤0.5%, Ti is 0.01% -0.30%, rare earth metals 0.01-2.5%, Pb ≤ 0.1%, Sn ≤ 0.01%, Cd ≤ 0.01%, the sum of other impurities is not more than 0.3%; th...
Embodiment 1
[0058] Raw material ratio
[0059] Raw material ratio, calculated by weight percentage, silicon: 0.038%, iron: 0.101%, copper: 0.0008%, manganese: 1.24%, magnesium: 0.0013%, zinc: 0.018%, titanium: 0.054%, lanthanum: 0.15%, lead: 0.0005%, tin: 0.001%, cadmium: 0.0011%, other impurities total and not more than 0.3%; the balance is aluminum.
[0060] Clean up and check for furnace residue on the walls and floor of the furnace. Feed 88% of the weight of electrolytic aluminum ingots into the furnace. Heat and melt to become molten aluminum and raise the temperature to 866°C, add manganese element additives, and then add titanium element additives after melting, mechanically stir with graphite after melting, and alternate with net placement 4 times, each time for 12 minutes, to make it effective Alloying. Then put the remaining 12% electrolytic aluminum ingot weight into the furnace, and use graphite for mechanical stirring after melting. Lower the temperature of the molten alu...
Embodiment 2
[0064] Raw material ratio
[0065] Raw material ratio, calculated by weight percentage, silicon: 0.037%, iron: 0.089%, copper: 0.0003%, manganese: 1.23%, magnesium: 0.001%, zinc: 0.016%, titanium: 0.064%, lanthanum: 0.19%, lead: 0.0018%, tin: 0.001%, cadmium: 0.0009%, other impurities total and not more than 0.3%; the balance is aluminum.
[0066] Clean up and check for furnace residue on the walls and floor of the furnace. Feed 88% of the weight of electrolytic aluminum ingots into the furnace. Heat and melt to become aluminum liquid and raise the temperature to 853°C, add manganese element additives, and then add titanium element additives after melting, mechanically stir with graphite after melting, and alternate with net placement for 5 times, each time for 10 minutes, to make it effective Alloying. Then put the remaining 12% electrolytic aluminum ingot weight into the furnace, and use graphite for mechanical stirring after melting. Lower the temperature of the molten ...
PUM
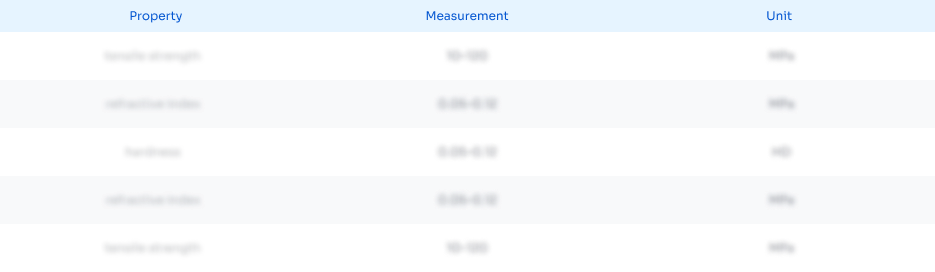
Abstract
Description
Claims
Application Information

- R&D
- Intellectual Property
- Life Sciences
- Materials
- Tech Scout
- Unparalleled Data Quality
- Higher Quality Content
- 60% Fewer Hallucinations
Browse by: Latest US Patents, China's latest patents, Technical Efficacy Thesaurus, Application Domain, Technology Topic, Popular Technical Reports.
© 2025 PatSnap. All rights reserved.Legal|Privacy policy|Modern Slavery Act Transparency Statement|Sitemap|About US| Contact US: help@patsnap.com