A Coal Caving Technology with Interval and Equal Caving in Combined Caving in Extra-thick Coal Seam
A technology of extra-thick coal seam and process, applied in the field of coal mining, can solve the problems of difficulty in coal drawing, waste, and high gangue content of raw coal
- Summary
- Abstract
- Description
- Claims
- Application Information
AI Technical Summary
Problems solved by technology
Method used
Image
Examples
Embodiment 1
[0032] Such as image 3 and 4 As shown, a coal caving process with equal intervals for joint caving of extra-thick coal seams includes the following steps:
[0033] S1. Grouping of hydraulic supports: when caving in extra-thick coal seams, first group the hydraulic supports into groups of three, and label them sequentially;
[0034] S2. Coal discharge in groups:
[0035] a. First, open the coal outlets of the first group of odd groups of hydraulic supports from the side. After the coal close to the supports is discharged, the upper coal sinks, and the gangue also falls to fill the top space, and the top coal is put on the top. During the process, the coal is transported away by the scraper conveyor until the coal seam drops to 1 / 3-1 / 2 of the thickness of the original coal seam, and the coal discharge port of the group of hydraulic supports is closed;
[0036] b. Open the coal outlets of the odd groups of hydraulic supports adjacent to the previous group of hydraulic support...
Embodiment 2
[0043] Such as Figure 5 As shown, a coal caving process with equal intervals for joint caving of extra-thick coal seams includes the following steps:
[0044]S1. Grouping of hydraulic supports: when caving in extra-thick coal seams, first group the hydraulic supports into groups of two in odd groups and three in even groups, and label them sequentially;
[0045] S2. Coal discharge in groups:
[0046] a. First, open the coal outlet of the first group of odd groups of hydraulic supports at the edge, and transport the coal through the scraper conveyor during the top coal caving process until the coal seam drops to 1 / 2-2 / 3 of the thickness of the original coal seam Close the coal discharge port of this group of hydraulic supports after hours;
[0047] b. Open the coal outlets of the odd groups of hydraulic supports adjacent to the previous group of hydraulic supports for coal discharge. During the top coal caving process, the coal is transported away by the scraper conveyor unt...
Embodiment 3
[0054] Such as figure 1 and 2 As shown, the coal discharge process includes the following steps:
[0055] Open the coal outlet of the single-frame hydraulic support, let the top coal flow out from the coal outlet, and close the coal outlet when the gangue on the roof is seen falling, and then press as follows figure 2 In the shown manner, the coal outlet of the adjacent single-frame hydraulic support is opened, and the coal is discharged again, and the coal discharge is stopped when gangue is encountered, and so on, until all the coal is released.
PUM
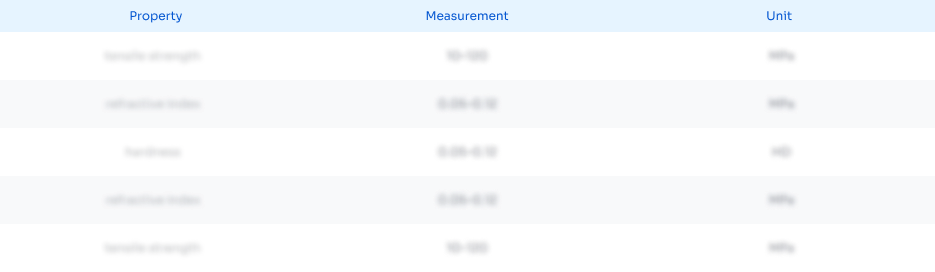
Abstract
Description
Claims
Application Information

- R&D
- Intellectual Property
- Life Sciences
- Materials
- Tech Scout
- Unparalleled Data Quality
- Higher Quality Content
- 60% Fewer Hallucinations
Browse by: Latest US Patents, China's latest patents, Technical Efficacy Thesaurus, Application Domain, Technology Topic, Popular Technical Reports.
© 2025 PatSnap. All rights reserved.Legal|Privacy policy|Modern Slavery Act Transparency Statement|Sitemap|About US| Contact US: help@patsnap.com